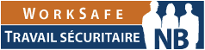
Asbestos
Asbestos is a naturally occurring mineral composed of flexible fibers that are resistant to heat, electricity and corrosion. Asbestos comes in many shapes, sizes, and finishes. These properties made the mineral useful in past construction applications, but asbestos exposure is highly toxic. Asbestos-containing materials (ACM) used over the past 80 years present potential health hazards for employees in some workplaces, and for those who may have been exposed by working on or near some machines, transportation vehicles, and vessels (train cars, boats, powered equipment, etc.).
Employees can be exposed to asbestos fibres when asbestos fibres they are released into the air as dust when the material is disturbed or handled and becomes respirable. A person exposed to asbestos may feel no ill effects at the time of exposure as there is a latency period between exposure and the development of a disease – which can range from 15 to 55 years. WorkSafeNB has created a guide to explain the risk from asbestos, where to find asbestos, and the legislated obligations around asbestos. (Asbestos Guide - ‘’Does your workplace contain asbestos?’’)
Asbestos Testing
One misconception is that you only need to test for asbestos when planning demolitions or renovations. In reality, the law requires that the asbestos Code of Practice (CoP) be followed whenever there are any employees working in proximity to material containing asbestos or suspected of containing asbestos. WorkSafeNB developed the Code of Practice to provide safe handling procedures to help minimize exposure to asbestos. It protects employees who are working in proximity to, or handling ACMs.
In New Brunswick, employers have a legal obligation to protect the health and safety of employees in the workplace. This duty includes the requirement for building owners to test if their building or workplace contains asbestos. Samples of suspected ACM must be sent to a specialized laboratory.
Asbestos is regulated by the General Regulation 91-191 under The Occupational Health and Safety Act.
Visual inspection and checking building records may not be adequate to establish if asbestos is present. The only reliable method to identify asbestos is by microscopic analysis. When in doubt, it is best to assume the building contains asbestos until proven otherwise. Consequently, the building should be assessed or inspected by a competent person to determine if any ACM is present.
It is critical that bulk sampling of suspected materials in buildings is carried out properly, and that laboratory analyses are performed accurately to determine if ACM is present. Sampling must be collected by a competent person and must include the correct number of samples for the room size.
In most cases, you should assume buildings constructed before 1990 contain ACM. But some construction materials containing asbestos were being used up until 1999. It is therefore necessary for building owners and employers to perform inspections and bulk sample analyses. Keep records to document the type, location, and the condition of the ACM, especially before demolishing or altering these buildings.
What should you do if you find asbestos at work?
Owners and Employers
If ACM is determined to be present (measured as greater than 1% by volume), owners, employers and contractors must adopt and follow the Code of Practice for Working with Materials Containing Asbestos in New Brunswick. WorkSafeNB developed this Code of Practice to help minimize the exposure to asbestos while the ACM remains in the workplace and to provide the requirements for abatement, encapsulation, training, and notifications.
Following this Code of Practice will protect employees who are working in proximity to, or handling ACMs. Once ACM is confirmed to be in the building, owners and employers must prepare a written inspection report that contains:
- the type and concentration by volume of asbestos (when it is present by 1% or more by volume)
- drawings, plans and specifications, as appropriate, to show the location of the ACM, and
- documentation about the condition of the ACM and any repairs or other corrective action required.
This written report must be made available to all involved before any work is done that may disturb ACM. This information must also be communicated to contractors before building renovations or any demolition is undertaken.
Asbestos Management Program
The owner and employer will need to decide if they are going to remove the ACM or leave it in place. This decision will depend on the type, percentage, and the condition of the materials. If the ACM presents a hazard due to its condition, it must be repaired or removed.
While the ACM remains in the building, owners, contractors and employers must develop and maintain an Asbestos Management Program (AMP). The Code of Practice includes the steps owners, contractors and employers must take to develop, implement, and maintain an Asbestos Management Program. . This program must also be shared with all employees in the building. WorkSafeNB has developed a template (see the Asbestos guide) to help owners and employers to establish their AMP. The employer must develop this AMP in consultation with the Joint Health and Safety Committee or Health and Safety representatives if they exist in the workplace.
If any renovations or demolition are planned in the building, owners and employers must inform employees (including any external contractors) of the existence of this AMP and communicate to these individuals any material or areas which were not tested. These parties would include any abatement company who may have been hired to remove or encapsulate the asbestos.
Employers and supervisors must ensure the AMP has been shared with employees and that they are following the procedures.
Depending on the level of risk, operations have been divided into three different classes:
The employer shall ensure employees follow the procedures also according to the level of risk.
Employees
If any ACM (or suspected ACM) is damaged, employees must:
- be made aware that all tasks must be stopped
- not to disturb the ACM
- protect themselves with appropriate PPE
- leave the area
- immediately report it to their supervisor for testing and confirmation.
General Regulation - Occupational Health and Safety
Act
N.B. Reg. 91-191
Part III.1 CODE OF PRACTICE FOR ASBESTOS
Section 25.3 Definition of "asbestos"
25.3 In this Part, "asbestos" means any of the following fibrous silicates:
(a) chrysotile;
(b) amosite;
(c) crocidolite;
(d) actinolite;
(e) anthophyllite; and
(f) tremolite.
[N.B. Reg. 2022-27, s. 17]
Section 25.4 Code of practice
25.4 (1) An owner of a place of employment, an employer and a contractor shall each adopt, for employees who work with, in proximity to or disturb material containing asbestos, the code of practice entitled "A Code of Practice for Working with Materials Containing Asbestos in New Brunswick" prepared by and amended from time to time by the Commission.
(2) An owner of a place of employment, an employer and a contractor shall each follow the code of practice referred to in subsection (1) and shall ensure that employees follow the code of practice.
[N.B. Reg. 2022-27, s. 17]
Code of Practice for Working with Materials Containing
Asbestos in New Brunswick
April 2022
Part 3 INSPECTION AND DETERMINATION OF ASBESTOS
Section 3.2
3.2 For the purposes of this Code of Practice, an acceptable procedure for establishing whether asbestos is present in material is as follows:
(a) Unless the owner of a place of employment, an employer and contractor deems the work area as containing asbestos, samples for testing will be collected by a competent person as follows:
(i) 100 square feet (9.3 m2) - or less - at least one sample;
(ii) 101 square feet (9.4 m2) to 1000 square feet (93 m2) - at least three samples;
(iii) 1001 square feet (93 m2) to 5000 square feet (465 m2) - at least five samples;
(iv) greater than 5000 square feet (465 m2) - at least seven samples;
(b) Separate samples should be taken where there is a difference in the texture or color of the material.
(c) A small container can be used, such as a plastic 35 mm film canister, a small wide-mouth glass jar with a screw-on lid, or a re-sealable plastic bag. The container should be dry and clean.
(d) The material from which the sample is drawn should not be otherwise disturbed or damaged.
(e) The area around where the sample is collected should be sprayed with a light mist of water to prevent further damage and fibre release during collection.
(f) If a solid container is used, the open end of the container should be gently twisted into the material. A core of the material should fall into the container. A sample can also be taken by using a knife to cut out or scrape off a small piece of material, and then place it into the container. Be sure to penetrate any protective coating and all the layers of material.
(g) The sample container should be tightly closed. The exterior of the container should be wiped with a damp cloth to remove any material which may have adhered to it.
(h) The damaged areas should be repaired or sealed with encapsulant, a cover or otherwise protected to prevent further fibre release.
(i) Floors or other surfaces contaminated with debris generated during sample collection should be wiped clean with a damp cloth or HEPA vacuumed. Collected debris should be treated as asbestos waste.
(j) The container lid should be taped to prevent the accidental opening of the container during shipment or handling.
(k)The sample container shall be labelled to identify the location and the date the sample was taken, and include a unique identification number.
(l) A written record of each sample shall be made by noting the date the sample was taken, the location of the material sampled, the area or room sampled, and the identification number.
(m) The bulk sample(s) obtained shall be analyzed in a specialized laboratory where analyses can be conducted with precision.
(n) The request for analysis shall specify:
(i) Classification of the type of asbestos,
(ii) Per cent composition by volume of asbestos in the sample.
Section 3.3
3.3 Where, upon inspection and bulk sampling, any material has been found to contain asbestos, the owner of a place of employment, employer and a contractor shall prepare an inspection report in writing containing:
(a) the type and per cent of asbestos;
(b) drawings, plans and specifications, as appropriate, to show the location of the asbestos material; and
(c) the report shall document the condition of the asbestos-containing material and any repairs or other corrective action required.
Part 4 ASBESTOS MANAGEMENT PROGRAM
Section 4.1
4.1 Where it has been established by inspection, bulk sample analysis, or deemed by an owner of a place of employment, an employer or contractor that material containing asbestos has been used in a building, an owner of a place of employment, an employer and a contractor shall ensure that an asbestos management program is developed in writing and maintained while the asbestos-containing materials remain in the workplace.
Section 4.2
4.2 The asbestos management program referred to in subsection 4.1 shall be developed in consultation with the Joint Health and Safety Committee (if any) or the health and safety representative.
Section 4.3
4.3 The asbestos management program shall address the following elements:
(a) Safe procedures as required in sections 5, 6 and 7 to ensure that the damaged asbestos-containing material is cleaned up and removed;
(b) Safe procedures for the repairing, sealing, removing or permanently enclosing the asbestos-containing material where it has been determined that the material will continue to deteriorate;
(c) Records of location where asbestos-containing material is found;
(d) Communication procedures to notify in writing anyone who may be at or adjacent to the location of the asbestos material and advise them not to disturb it;
(e) Identification system for asbestos-containing material using colour coding, labels, placards or any other mode of identification;
(f) Procedures for inspection of the asbestos material at least once per year, in order to determine its condition;
(g) Provisions for the education, training and instruction for every employee in the building who is likely to work in close proximity to and may disturb the asbestos-containing material; and
(h) The education, training and instruction program in (g) shall include, but not limited to:
(i) the hazards of asbestos exposure;
(ii) the use, care and maintenance of required protective equipment, including personal protective equipment and clothing.
(iii) the work practices and procedures to be used in doing the work as prescribed by this Code of Practice;
(iv) the disposal procedures for asbestos contaminated materials; and
(v) personal hygiene.
Section 4.4
4.4 Where respirators are required to be worn by employees, the employer and employee shall comply with the provisions of Section 45 to 47 of Regulation 91-191 .
Part 5 LOW RISK - OPERATIONS AND PROCEDURES
Section 5.1 Low Risk - Operations
5.1 For the purposes of this Code of Practice, operations under Low Risk are:
(a) the installation or wet removal of manufactured products containing asbestos, including products such as vinyl or acoustic tiles, gaskets, seals, packing, friction products, or asbestos cement products;
(b) the opening of ceiling tiles for inspection purposes;
(c) the opening of brake drums, and replacement or repair of brake pads;
(d) repair or replacement of clutches; and
(e) handling of asbestos waste that has been double bagged.
Section 5.2 Low Risk- Procedures
5.2 An owner of a place of employment, an employer and a contractor shall ensure that the following procedures applying to Low Risk operations are complied with:
(a) before beginning work, visible dust is removed with a damp cloth or a vacuum equipped with a HEPA filter, from any surface in the work area, including the surface to be worked on, if the dust on that surface is likely to be disturbed;
(b) the spread of asbestos dust from the immediate work area is controlled by measures appropriate to the work to be done, which may include the use of drop sheets of polyethylene or other suitable material;
(c) compressed air hoses are not used to clean;
(d) NIOSH approved N95 disposable respirators (or better), or a Standard offering equivalent protection, are made available for use by employees;
(e) waste material is discarded according to the requirements of the New Brunswick Department of the Environment and Local Government; and
(f) waste material is transported in accordance with the Transportation of Dangerous Goods Act .
Part 6 MODERATE RISK - OPERATIONS AND PROCEDURES
Section 6.1 Moderate Risk - Operations
6.1 For the purposes of this Code of Practice, operations classified under Moderate Risk are:
(a) the removal of a false ceiling, or part of it, to obtain access to a work area, where a significant quantity of friable material containing asbestos is likely to be lying on the surface of the false ceiling;
(b) the minor removal or minor disturbance (less than 30 square feet (2.8 m2) of surface area) of friable material containing asbestos during the repair, alteration, maintenance or demolition of a building, aircraft, ship, locomotive, railway car or vehicle, or any machinery or equipment;
(c) the application of tape or a sealant or other covering to pipe or boiler insulation containing asbestos;
(d) the removal of pipe insulation containing friable asbestos with the help of a commercial containment bag (glove bag);
(e) the enclosure of asbestos-containing material;
(f) the use of a power tool having a dust collection device equipped with a HEPA filter to cut, grind or abrade a product mentioned in paragraph 5.1(a);
(g) the cutting, drilling or shaping of a product mentioned in paragraph 5.1(a) by the use of hand operated tools;
(h) the removal of drywall where asbestos joint-filling compounds have been used;
(i) the clean-up of small quantities of friable asbestos debris that has detached from insulation;
(j) the dry removal of manufactured products containing asbestos, including products such as vinyl or acoustic tiles, gaskets, seals, packing, friction products, or asbestos cement products;
(k) any encapsulation work where the actual damaged area of the entire encapsulation project is less than 30 square feet (2.8 m2);
(l) removal of vinyl asbestos floor coverings; and
(m) any operation not mentioned in paragraphs (a) to (l) that may cause exposure of an employee to asbestos, and that is not classified as a Low Risk or a High Risk operation.
Section 6.2.1
6.2.1 The owner of a place of employment, an employer and a contractor shall ensure that:
(a) amended water is used to control the spread of asbestos dust, unless wetting creates a hazard or causes damage;
(b) eating, drinking, chewing or smoking is not permitted in the work area;
(c) no person shall enter the work area unless they are wearing proper protective equipment;
(d) every employee who enters the work area is provided with NIOSH approved, or a Standard offering equivalent protection, N, R or P100, reusable, air purifying respirators (or better);
(e) protective clothing is provided to every employee who enters the work area, and that:
(i) the protective clothing consists of full body covering, including head covering, with snug-fitting cuffs at the wrists, ankles and neck, and footwear;
(ii) it is repaired or replaced if torn;
(iii) it is left inside the work area, or is decontaminated using a vacuum equipped with a HEPA filter before leaving the contaminated work area; and
(iv) it is discarded as asbestos contaminated material, (or washed if reusable), upon completion of the removal project;
(f) facilities for washing hands and face are made available to an employee, and are used by every employee, when leaving the work area;
(g) the work area is identified by clearly visible signs warning of the asbestos-dust hazard;
(h) compressed air is not used to clean;
(i) before commencing work that is likely to disturb friable material containing asbestos that is crumbled, pulverized or powdered, and that is lying on any surface, the friable material is cleaned up and removed by damp-wiping, or by using a vacuum equipped with a HEPA filter;
(j) the spread of asbestos-dust from the work area is prevented, by
(i) an enclosure of polyethylene or other suitable material thick enough to withstand wear and tear where walls do not enclose the work area;
(ii) the use of drop sheets; and
(iii) disabling the mechanical ventilation system serving the work area, and by sealing the ventilation ducts to and from the work area;
(k) frequently and regularly during the work, and immediately upon completion,
(i) dust and waste containing asbestos is cleaned up and removed by damp-mopping, and placed in a suitably lined container or a six mil polyethylene bag or by using a vacuum equipped with a HEPA filter;
(ii) drop sheets and barriers that are to be reused are thoroughly cleaned;
(l) drop sheets and barriers that are to be discarded are considered and treated as asbestos contaminated material; and
(m) waste materials, including discarded polyethylene sheeting, sealing tape, cleaning materials, protective clothing, vacuum bags, and other contaminated materials, are
(i) double bagged in a six mil polyethylene bag and identified as containing asbestos. Label must also state hazards of exposure to asbestos, precautionary statements and handling required;
(ii) secured against unauthorized removal or damage;
(iii) transported in accordance with the Transportation of Dangerous Goods Act ; and
(iv) discarded according to the requirements of the New Brunswick Department of the Environment and Local Government.
Part 7 HIGH RISK - OPERATIONS AND PROCEDURES
Section 7.1 High Risk - Operations
7.1 For the purposes of this Code of Practice, operations classified under High Risk are:
(a) the removal of 30 square feet (2.8 m2) or more, of friable material containing asbestos during the repair, alteration, maintenance or demolition of a building, aircraft, ship, locomotive, railway car or vehicle, or any machinery or equipment or part thereof;
(b) the spray application of a sealant to friable material containing asbestos;
(c) the cleaning or removal of air-handling equipment, including rigid ducting, in a building that has sprayed-fireproofing containing asbestos;
(d) an outdoor operation involving the removal or stripping of friable asbestos-containing materials; and
(e) the repair, alteration or demolition of a kiln, metallurgical furnace or similar device or part thereof, made in part of refractory materials containing asbestos.
The owner of a place of employment, an employer or a contractor shall develop an emergency response procedure for use in the event of serious injury and other emergencies in the work area.
Section 7.2.1 Preparation
7.2.1 The owner of a place of employment , an employer and a contractor shall ensure that:
(a) signs are posted around the perimeter of the removal area to restrict access;
(b) the signs required in paragraph (a) are posted in sufficient numbers to warn of the hazard, and state in large clearly visible letters that
(i) there is an asbestos-dust hazard; and
(ii) access to the work area is restricted to persons wearing protective clothing and respiratory protective equipment;
(c) respiratory protection is worn by all employees on-site during the preparation of work areas for asbestos removal, where any disturbance of the material may occur;
(d) respiratory protection includes:
(i) a NIOSH approved P100 reusable air purifying respirator with a minimum protection factor of 10 or better when asbestos is not disturbed, or
(ii) a NIOSH approved P100 respirator with a minimum protection factor of 100 or better when asbestos is disturbed;
(e) the mechanical ventilation system serving the work area is rendered inoperative for the duration of the asbestos work to prevent contamination and fibre dispersal to other areas, by
(i) switching off the system where possible; and
(ii) sealing the ventilation ducts to and from the work area; or
(iii) where the ventilation system cannot be switched off, blanking off the main ventilation duct to the area with rigid impervious material such as metal or wood;
(f) all moveable equipment and material is removed from the work area;
(g) floors, walls and any items remaining in the room are sealed with polyethylene sheeting, and that
(i) the polyethylene on the floor shall be extended at least 12 inches (30 cm) up each wall and rip-stop poly shall be placed over the polyethylene on the floor;
(ii) any damage to the polyethylene sheeting that occurs as the work proceeds is repaired immediately;
(iii) the polyethylene sheeting has a minimum thickness of six mil; and
(iv if the enclosure is opaque, one or more transparent window areas are installed to allow observation of the entire work area from outside the enclosure,
(h) drop sheets are used during outdoor removal operations;
(i) every precaution is taken to avoid electric shock, including disconnection of electric power to permanent fixtures, except that temporary connections may be made for illumination purposes and for the operation of asbestos removal equipment;
(j) the electrical equipment used in wet removal operations is
(i) battery operated;
(ii) double insulated;
(iii) bonded to ground, extra low voltage, not exceeding 30 volts and 100 volt-amps; or
(iv) bonded to ground, and equipped with a ground fault circuit interrupter of the Class A type, which is tested before each use;
(k) a decontamination area is set up adjacent to the work area which consists of:
(i) a clean changing room suitable for changing into clean protective clothing or street clothes, and for storing clean clothing and equipment;
(ii) a shower room as described in paragraph (m);
(iii) a room suitable for donning reusable protective clothing, and for storing contaminated protective clothing and equipment;
(l) air lock doors are provided and used between the different rooms, and that
(i) they consist of layers of polyethylene with at least a three foot (1 m) overlap,
(ii) these sheets are weighted at the bottom to keep the flaps closed,
(iii) they are arranged in sequence, and
(iv) they are constructed so as to prevent the spread of asbestos dust;
(m) the shower room in the decontamination facility
(i) is located between the contaminated change room and the clean change room,
(ii) is provided with hot and cold water, or water of a constant temperature that is not less than 40o Celsius or more than 50o Celsius,
(iii) has controls inside the room to regulate water flow and temperature,
(iv) is capable of providing an adequate supply of hot water to maintain a water temperature of at least 40o Celsius, and
(ame as 5.2v) is provided with clean towels;
(n) adequate toilet facilities exist in the work area, or that where such facilities do not exist in the work area, employees go through the proper decontamination sequence before going to the toilet facilities; and
(o) once the enclosure has been established, a competent person must verify the integrity of the containment and the effectiveness of the negative air system. A record of this inspection must be maintained as part of the project records.