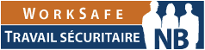
Elevating Work Platforms
Elevating work platforms may be a hazard for employees when not used, maintained, or stored adequately. Manufacturer's instructions and limitations of the equipment must be followed. To prevent injuries multiple factors must be considered, such as:
- Does the equipment have the lifting capacity?
- What is the condition of the surface?
- Does the operator have the knowledge and training to carry out the task safely?
Other factors include the weather, obstructions, materials to be lifted, and other employees working near the equipment.
Common hazards include the machine tipping or overturning, overriding safety features, working near power lines, overloading the platform, contact by passing equipment or traffic, contact from swinging booms or pinched by scissor mechanisms, poor maintenance, unauthorized modifications, or unauthorized access on the equipment.
Four types of elevating work platforms are covered in this guide:
- Portable Elevating Work Platforms (commonly referred to as scissor lifts)
- Self-Propelled Elevating Work Platforms. (commonly referred to as scissor lifts)
- Self-propelled Boom Supported Elevating Work Platforms (commonly referred to as zoom booms)
As an employer, you must:
- Ensure that an elevating work platform is designed, constructed, erected, maintained, inspected, monitored and used in accordance with the following CSA standards, or a standard offering equivalent or better protection, where applicable:
- Provide and ensure that employees use a travel restraint system or fall-arresting system when working from a scissor lift.
- Fall arrest or fall restraint is not required when the equipment:
- Is on a firm and flat surface.
- Has all the manufacturer's guardrails and chains in place.
- Is not moving horizontally or vertically.
- Ensure your employees use a travel restraint system or fall-arresting system attached to an anchor on the machine when required to work from a zoom boom.
- Ensure the operator conducts inspections before using the equipment and it is inspected as recommended by the manufacturer.
- Ensure only competent personnel operate and inspect an elevating work platform.
- Ensure the procedure to lower the equipment in case of an emergency is well understood and is working properly.
- Ensure that labels and decals are clearly visible and readable and that the owner’s manual is on the equipment.
- Make modifications only with written permission by the manufacturer.
- Take equipment with deficiencies out of service.
- Not allow the equipment to be used in high wind.
- Ensure extension cords are long enough and won’t get pinched or severed by the scissor mechanism.
- Ensure that operators keep a minimum safe clearance of power lines:
Electrical utility line/equipment voltage | Safe distance |
---|---|
0 to 750 volts | (.9 m) 3 feet |
751 to 100,000 volts | (3.6 m) 12 feet |
100,001 to 250,000 volts | (5.2 m) 17 feet |
250,001 to 345,000 volts | (6.1 m) 20 feet |
While the employer is ultimately responsible for all the provisions mentioned above, the supervisor has a vital role to play in the safety of their teams. As a supervisor, you must:
- Acquaint your employees with the hazards and control measures associated with their work
- Provide the information and instruction necessary to ensure their health and safety
- Enforce company safety rules, programs, codes of practice and procedures, including ensuring employees comply with the requirements below.
As an operator, you must:
- Follow any instruction, education and training in operating an elevating work platform.
- Use required equipment including personal protective equipment such as a travel restraint system or fall arrest system.
- Be aware of changing conditions.
- Report to your employer or supervisor any known hazards.
Viewing CSA Standards as Referenced in NB Legislation
Certain CSA standards are available for online viewing or purchase from the CSA Group.
To access these, you must first create an account with CSA Communities
Once you are logged in, click on the "OHS Standards / View Access" option.
Click on New Brunswick to see the CSA Standards as referenced in N.B. legislation.
“competent” means
- (a) qualified, because of such factors as knowledge, training and experience, to do assigned work in a manner that will ensure the health and safety of persons,
- (b) knowledgeable about the provisions of the Act and the regulations that apply to the assigned work, and
- (c) knowledgeable about potential or actual danger to health or safety connected with the assigned work
General Regulation - Occupational Health and Safety
Act
N.B. Reg. 91-191
Part XI TEMPORARY STRUCTURES
Section 130 Elevating Work Platforms
130. (1) An employer shall ensure that an elevating work platform is designed, constructed, erected, maintained, inspected, monitored and used in accordance with the following CSA standards, where applicable:
(a) CAN/CSA-B354.1-04 (R2016), Portable elevating work platforms or a standard offering equivalent or better protection;
(b) CAN/CSA-B354.2-01 (R2013), Self-Propelled Elevating Work Platforms or a standard offering equivalent or better protection; and
(c) Repealed. [N.B. Reg. 2024-38, s. 67]
(d) CAN/CSA-B354.4-02 (R2013), Self-propelled boom-supported elevating work platforms or a standard offering equivalent or better protection.
(2) If an employee is required to work from an elevating work platform described in paragraph (1)(b), the employer shall provide and the employee shall continually use a travel restraint system or fall-arresting system attached to an anchor point on the elevating work platform.
(3) Despite subsection (2), an employee is not required to continually use a travel restraint system or fall-arresting system when an elevating work platform
(a) is on a firm and flat surface,
(b) has all the manufacturer's guardrails and chains in place, and
(c) is not moving horizontally or vertically.
[N.B. Reg. 2001-33, s. 41; 2010-159, s. 26; 2024-38, s. 67]