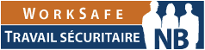
Workplace Inspections
Workplace inspections are an important prevention tool that can prevent injuries and illnesses and ensure that your health and safety program is working. The goal is to find any unsafe acts or conditions and implement necessary controls.
A program for inspecting the entire workplace at least once a month must be developed with the joint health and safety committee (JHSC) or health and safety (H&S) representative. The workplace can be divided into sections, each with its own inspection person or team. Inspections may also be scheduled daily, weekly, monthly or annually or at other frequencies depending on the nature of the issue, requirements of legislation and the regulations (for example, a lift truck must be inspected daily ), or as recommended by equipment manufacturers. You can also use your hazard identification system and incident history to help identify areas that may require more frequent inspections. Ideally inspections should be done on a schedule that will prevent the development of unsafe conditions.
There are four main types of inspections:
- Formal (Planned) - normally done by using a written checklist and carried out by a team at regular intervals.
- Informal (On the spot) - done by management, supervisors and JHSC or H&S representatives by observing the area for unsafe acts and conditions, and noting the issues in the daily log or by completing a simple form.
- Specialized inspections - conducted by specialists (for example on boilers, electrical equipment, mechanical or ventilation systems).
- Regulatory - normally consists of inspections required by the OHS regulations. Examples include inspection of fall protection equipment.
Note: The scope of this OHS Guide is to address formal or planned inspections.
An inspection team should include both employee and employer representatives. They should be familiar with the work process and, whenever possible, include members of the JHSC or H&S representative.
Formal or planned inspections should be done using a formal checklist, tailored to the workplace's needs. Items on the checklist should not be considered permanent as incidents, changes in process, and near misses may result in new items being added to the checklist. A sample checklist is provided as an example.
Identified hazards must be classified, using a hazard classification system; this will ensure that hazards are addressed by rankings. An example is provided at the end of the sample checklist.
As an employer, you must:
- Include the procedures and schedules for inspections in the hazard identification system when a health and safety program is required in the workplace.
- Ensure that the place of employment is inspected at least monthly to identify any risks to employee health and safety.
- Develop a program for the inspection with the JHSC or the H&S representative and share the results of each inspection with the JHSC or the H&S representative.
- Train employees to regularly inspect their machinery, tools, and equipment.
- Ensure that inspection results are recorded and significant findings are acted on.
The steps to follow for a successful inspection include:
- Planning your route and any primary concerns to be observed.
- Observing tasks being done.
- Asking questions, making notes.
- Examining equipment, checking maintenance records.
- Checking that the work area is tidy and that tools have a storage place.
- Looking for what might not be obvious such as fire doors not opening outward or being blocked.
- Establishing clear procedures that identify when and how often to conduct each inspection. Some tasks may require daily or start-of-shift inspections. Record who will do them and who will follow up.
- While the workplace requires monthly inspections, more frequent inspections may be required and a schedule should be established based on the frequency of work, degree of hazard, and a history of incidents or near misses.
- Keeping records of all inspections, findings, recommendations and follow-up.
- Ensuring the JHSC (or H&S representative) sees the reports and follow-up.
Following the minimum monthly inspections on constantly changing workplaces, like a construction site, will not be sufficient to identify unsafe acts and conditions as they develop.
Could also be used to follow-up on corrective actions identified during the formal or planned inspection, after a near miss, an incident, installation of a new piece of equipment, a change in a work process or procedure, etc.
OCCUPATIONAL HEALTH AND SAFETY ACT
S.N.B. 1983, c. O-0.2
DUTIES OF EMPLOYERS, OWNERS, CONTRACTORS, SUB-CONTRACTORS, SUPERVISORS, EMPLOYEES AND SUPPLIERS
Section 8.1
8.1 (1) Every employer with 20 or more employees regularly employed in the Province shall establish a written health and safety program, in consultation with the committee or the health and safety representative, that includes provisions with respect to the following matters:
(a) the training and supervision of the employees in matters necessary to their health and safety;
(b) the preparation of written work procedures and codes of practice for the implementation of health and safety work practices, required by this Act, the regulations or by any order made in accordance with this Act;
(c) the identification of the types of work for which the work procedures are required at the places of employment of the employer;
(d) a hazard identification system that includes
(i) evaluation of the place of employment to identify potential hazards,
(ii) procedures and schedules for inspections, and
(iii) procedures for ensuring the reporting of hazards, prompt follow-up and control of the hazards;
(e) a system for the prompt investigation of hazardous occurrences to determine their causes and the actions needed to prevent recurrences;
(f) a record management system that includes reports of employee training, accident statistics, work procedures and health and safety inspections, maintenance, follow-up and investigations; and
(g) monitoring the implementation and effectiveness of the program.
(2) The employer shall review its health and safety program at least once each year, in consultation with the committee or the health and safety representative, and shall update the program as required.
(3) The employer shall make a copy of the program and all records available
(a) to the committee or the health and safety representative, and
(b) on request, to an employee at the place of employment or the Commission.
[S.N.B. 2013, c. 15, s. 3]
Section 9 Duties of employer
9. (1) Every employer shall
(a) take every reasonable precaution to ensure the health and safety of his employees;
(b) comply with this Act, the regulations and any order made in accordance with this Act or the regulations; and
(c) ensure that his employees comply with this Act, the regulations and any order made in accordance with this Act or the regulations.
(2) Without limiting the generality of the duties under subsection (1), every employer shall
(a) ensure that the necessary systems of work, tools, equipment, machines, devices and materials are maintained in good condition and are of minimum risk to health and safety when used as directed by the supplier or in accordance with the directions supplied by the supplier;
(a.1) ensure that the place of employment is inspected at least once a month to identify any risks to the health and safety of his employees;
(b) acquaint an employee with any hazard in connection with the use, handling, storage, disposal and transport of any tool, equipment, machine, device or biological, chemical or physical agent;
(c) provide the information that is necessary to ensure an employee’s health and safety;
(c.1) provide the instruction that is necessary to ensure an employee’s health and safety;
(c.2) provide the training that is necessary to ensure an employee’s health and safety;
(c.3) ensure that work at the place of employment is competently supervised and that supervisors have sufficient knowledge of all of the following with respect to matters that are within the scope of the supervisor’s duties:
(i) this Act and any regulations under this Act that apply to the place of employment;
(ii) any safety policy for the place of employment;
(iii) any health and safety program for the place of employment;
(iv) any health and safety procedures with respect to hazards in connection with the use, handling, storage, disposal and transport of any tool, equipment, machine, device or biological, chemical or physical agent by employees who work under the supervisor’s supervision and direction;
(v) any protective equipment required to ensure the health and safety of the employees who work under the supervisor’s supervision and direction; and
(vi) any other matters that are necessary to ensure the health and safety of the employees who work under the supervisor’s supervision and direction;
(c.4) ensure that work at the place of employment is sufficiently supervised;
(d) provide and maintain in good condition such protective equipment as is required by regulation and ensure that such equipment is used by an employee in the course of work;
(e) co-operate with a committee, where such a committee has been established, a health and safety representative, where such a representative has been elected or designated, and with any person responsible for the enforcement of this Act and the regulations.
(3) An employer shall develop a program for the inspection referred to in paragraph (2)(a.1) with the joint health and safety committee, if any, or the health and safety representative, if any, and shall share the results of each inspection with the committee or the health and safety representative.
[S.N.B. 2001, c. 35, s. 3; 2007, c. 12, s. 2; 2013, c. 15, s. 4; 2019, c. 38, s. 4]
General Regulation - Occupational Health and Safety Act
N.B. Reg. 91-191
Part XV MATERIALS HANDLING EQUIPMENT AND PERSONNEL CARRYING EQUIPMENT
Section 216 Industrial Lift Trucks
216. (1) An employer shall ensure that an industrial lift truck
(a) is used only for the purposes for which it was designed,
(b) is operated by a competent employee,
(c) is inspected daily and maintained in good operating condition,
(d) is equipped with adequate brakes,
(e) is equipped with a manually operated horn,
(f) is equipped with adequate head and tail lights when used after dark or in dimly lit areas,
(g) is equipped with an audible back-up alarm that operates automatically when the truck is in reverse gear and that is clearly audible above the background noise at the place of employment, or a flashing light that operates automatically when the truck is in reverse gear and that is clearly visible to persons who may be at risk when the truck backs up,
(h) is equipped with overhead guards that conform to ANSI standard ASME B56.1-1993, "Safety Standard for Low Lift and High Lift Trucks" to protect the operator of the truck from falling material,
(i) has the manufacturer's rated capacity posted in a conspicuous location on the truck,
(j) is not loaded beyond its capacity, and
(k) has any load on it stabilized and, when necessary, secured.
(2) An employer shall ensure that an industrial lift truck is not operated
(a) where propelled by an internal combustion engine, near areas containing explosive dusts or flammable vapours or in buildings where the ventilation is not sufficient to eliminate the hazards from exhaust gases,
(b) in a one-way aisle, unless the width of the aisle equals at least the width of the vehicle or load being carried, whichever is wider, plus 600 mm, or
(c) in a two-way aisle, unless the width of the aisle equals at least twice the width of the vehicle or load, whichever is wider, plus 900 mm.
(3) An employer shall install mirrors or other similar devices at blind intersections where there may be a danger of a collision between an industrial lift truck and another object or a person.
(4) Where a hazard exists from rolling over, an employer shall ensure that an industrial lift truck is equipped with a rollover protective structure that meets the minimum safety requirements of CSA standard B352.0-95 , "Rollover Protective Structures (ROPS) for Agricultural, Construction, Earthmoving, Forestry, Industrial, and Mining Machines - Part 1: General Requirements" or safety requirements that are certified by an engineer to provide equivalent or better protection.
(5) An employer shall ensure that an industrial lift truck that has been fitted with a rollover protective structure is provided with seat belts or restraining devices that meet the requirements of subsection 221(1).
(6) An operator of an industrial lift truck shall use the seat belts or restraining devices referred to in subsection (5) while the industrial lift truck is in motion.
[N.B. Reg. 2001-33, s. 71]