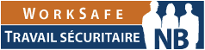
Ladders
Ladders are versatile, useful pieces of equipment used in all industry sectors. Ladders can be fixed or portable. They are mainly used for access type work, like reaching different levels above or below ground (roofs or trenches), and performance type work, such as fixing a light bulb or painting walls.
Falls from all sources, including ladders, are the second largest cause of accidental death in Canada. The proper training and use of the correct equipment will reduce the risks associated with ladders.
Most falls from ladders are traceable to three main problems:
- The wrong ladder was used.
- The ladder failed because it was in bad shape or the condition of the surface failed to support the ladder (slippery, unstable or uneven surfaces).
- The ladder was misused.
There are two types of ladders - fixed and portable. As an employer you must ensure the following:
- Ensure the fixed ladder is the right strength and length, clean and free from grease, maintained in a safe condition, properly secured at all points, and is constructed according to the regulation.
- Remove a fixed ladder from service when it has loose, broken or missing rungs, split side rails or other defects.
- Provide ladder cages for a fixed ladder that is more than 6 m in height, except where an employee uses a fall-arresting system.
- Ensure the ladder cage is constructed according to the regulation.
For portable ladders:
- Ensure that any portable ladder used at the workplace is of adequate strength and length, clean and free of grease, and maintained in a safe condition.
- Remove a portable ladder from service when it has loose, broken or missing rungs, split side rails or other defects.
- Ensure that wooden portable ladders are made of No. 1 grade or better spruce or fir, are not painted (other than preserved with a transparent protective coating), and have rungs and side rails built according to the regulations. Single ladders must not be longer than 6 m.
- Ensure that portable ladders comply with and are used according to the CSA Z11-12 (R2017), “Portable ladders” or ANSI ASC-14.7-2011, “Safety Requirements for Mobile Ladder Stand Platforms” or a standard offering equivalent or better protection.
- Ensure a portable extension ladder has no more than three sections, locks securely, and when extended, maintains the following overlaps:
- If the ladder is 11 m or less, the overlap must be 1 m.
- If the ladder exceeds 11 m and is 15 m or less, the overlap must be 1.25 m.
- If the ladder exceeds 15 m and is 22 m or less, the overlap must be 1.5 m.
- When an employee is working 3 m or higher on a portable ladder, the work may be done without a fall-protection system if:
- The work is light duty and of short duration at each location.
- The employee can maintain their centre of gravity between the ladder side rails.
- The employee can usually have one hand free to hold on to the ladder or another support, and (three point contact).
- The ladder is not near an edge or floor opening that would significantly increase the fall distance.
Special note: If you or your employees work around electricity, do not use an aluminum ladder, as it can conduct electricity when near the electrical lines. If it is not possible to use a non-conductive ladder, other precautions must be taken:
- Contact the authority owning or operating the electrical utility line or utility line equipment to ensure that the line or equipment is (a) de-energized or (b) adequately insulated or guarded before permitting any employees to start work.
- When an employee who is not a qualified person is about to start work that is liable to bring any person or object closer to an energized electrical line or utility line equipment, the employee must maintain the minimum distances specified in the table.
Phase to Phase Voltage of Energized Electrical Utility Line or Utility Line Equipment | Minimum Distance |
---|---|
Up to750 v | 900mm |
751 to100,000 v | 3.6m |
100,001 to 250,000 v | 5.2m |
250,001 to 345,000 v | 6.1m |
The minimum distances apply to all objects, including scaffolds, handtools, ladders, heavy equipment, etc. If in doubt, assume it is 750 volts or greater. |
[Source: WorkSafeNB Hazard Alert]
As an employer you also must:
- Train your employees on ladder safety. A ladder safety program should cover purchasing, selection, inspection, tag out, use, storage.
- Training should include:
- How to inspect ladders for defects before each use.
- How to select the right ladder for the task at hand (for example, the different ladders available for performance and access type work).
- Procedures for safe use of ladders near electricity by using ladders rated for near electrical work, such as those made from fibreglass.
- Correct set-up of extension ladders (follow the 1:4 rule: the base should be 1 foot from the wall for every 4 feet in height). Awareness that extension ladders must extend 1 m (3 feet) beyond the top resting point when used for climbing onto a platform.
- Correct tie-off of an extension ladder (rest both side rails on the top support, tie off ladder at the top and secure bottom to prevent it from slipping).
- The 3-point climbing method (maintain three point contact by keeping two hands and one foot, or two feet and one hand on ladder at all times).
- Provide necessary fall protection when working at heights above 3 m.
- Provide necessary warning signs and barricades and ensure employees use them to warn other employees when people are working on ladders.
- Review unsafe activities that lead to injuries:
- Do not lean from a ladder to reach work - reposition the ladder.
- Do not step on the top cap, the top rung, the bucket holder, or the back of the step ladder.
- Do not bring loads up, carry objects or tools in your hands. Use a sack strapped over the shoulder or otherwise secured to the person, or hoist it up or down using an appropriate method (lifting hoists, elevators, scissor lifts, etc.)
- Avoid climbing with wet footwear or rungs.
- Do not use a ladder in passageways, doorways, driveways or other locations where it can be hit. Erect suitable barricades or lock doors shut.
- Do not place a ladder against flexible or movable surfaces.
While the employer is ultimately responsible for all the provisions mentioned above, the supervisor has a vital role to play in the safety of their teams. As a supervisor, you must:
- Acquaint your employees with the hazards and control measures associated with their work
- Provide the information and instruction necessary to ensure their health and safety
- Enforce company safety rules, programs, codes of practice and procedures, including ensuring employees comply with the requirements below.
An employee must:
- Inspect the ladder before use.
- Report unsafe conditions to the employer or supervisor.
- Face the ladder and use both hands when climbing both up and down (three-point contact!).
- When on the ladder, stand in the centre between the side rails.
- Make sure the ladder is secured and will not move.
- Make sure the side rails of the ladder go at least 1 m above the platform or landing that you will step on.
- Make sure that legs on a step ladder are held securely by the brace or equivalent.
- Splice ladders together.
- Place a ladder in front or against a door, unless the door is blocked open, locked or guarded.
- Use a ladder as scaffold flooring, or to support scaffold flooring.
- Stand on the material shelf, the top cap, or the top rung.
- Work from the top three rungs of a portable single or extension ladder.
Proper selection and set-up
Choosing the right ladder is the first step to safety.
In Canada, new ladders are approved by the CSA Group and rated for how much load they can carry (heavy, medium, or light), and for the type of use (industrial, trade or household). Most ladders are made of wood, aluminum, or fibreglass. If you work around electricity, do not use an aluminum ladder, as it can conduct electricity when near the electrical lines.
Straight, extension and stepladders are known as portable ladders. Appendix A and Appendix B of CSA Standard Z11-12 (R2017), "Portable ladders" (or a standard that offers equivalent or better protection) provide additional information with respect to the proper selection, inspection, set-up, use, care, and storage of portable ladders. Straight and extension ladders are to be used against a wall, and normally for outdoor work. These ladders need to be placed very carefully; wrong setup is the single largest source of accidents. If the ladder slips at the base, you will fall. Safe ladder use includes:
- Placing the ladder on clear level ground free of ice, snow, water and sand.
- Following the 1:4 rule: the base should be 1 foot from the wall for every 4 feet in height.
- Not climbing above the fourth rung from the top of an extension ladder.
- If the ladder is used to access a flat roof for instance, it should rise about 1 m or 3 feet above that surface.
Stepladders - are common in workplaces and handy around the house. Safe ladder use includes:
- The spreader arms must be locked in the open position with all four legs evenly grounded.
- Staying off the top two rungs of a stepladder and using your knees for balance by resting them against the ladder.
- Never standing on top of the ladder or on the paint shelf.
- If you need a straight ladder, don't try and make a closed stepladder do the job.
Platform ladders - are larger metal ladders used in warehouses and industrial locations where good stability and a large flat work surface are needed.
Fixed ladders - adhere to the sides of buildings, tanks, and towers and must be equipped with a safety cage where it is more than 6 m in height, unless the employee on the ladder uses a fall-arresting system. Safe use of fixed ladders includes:
- Maintaining at least 165 mm clearance between the rungs and the structure to which the ladder is affixed.
- Fixing the ladder so that no rungs extend above a landing.
- Making sure a fixed ladder has side rails or other secure handholds that extend at least 1.07 m above the landing and are spaced not less than 685 mm apart.
- Removing the ladder from service when it has loose, broken or missing rungs, split side rails or other defects that may be hazardous to an employee.
Ship's ladders are a type of fixed ladder used in particular situations. A ship's ladder must:
- Be designed so the angle between the side rails and the horizontal is between 50° and 70°. The preferred angle is in the range of 60° to 68°.
- Serve only a single platform or landing and have a maximum height of 4 m (12 feet).
- Have tread width of at least 130 millimetres (mm) (5 inches), with a non-skid finish, uniformly spaced (rise) at no more than 305 mm (12 inches). Treads should be at least 430 mm (17 inches) long, but not longer than 630 mm (24 inches).
- Have a minimum design working load of 1.1 kilo newton (kN) (250 pounds) applied uniformly to a 90 mm (3.5 inch) strip across the centre of the tread.
- Have handrails provided on both sides of the ladder at approximately 900 mm (36 inches) above the tread nosing.
- Have a safety guard installed parallel to the slope of the ladder and offset approximately 150 mm (6 inches) from the rear of the treads. (This guard is to stop an employee's leg from passing through to the backside of the ladder if a foot slips off the back side of the tread.)
In addition, it should be noted that a ship's ladder is a permanent load-carrying structure and needs to be properly engineered. Design drawings and specifications should show all information necessary for the fabrication and installation of the ship's ladder, including details on how it is to be secured in place. The completed installation will need to be certified by a professional engineer as being fabricated and installed in accordance with good engineering practice.
Inspect the ladder
A ladder must also be cleaned, and maintained in good condition. Ladders don't last forever and should be looked over thoroughly before each use for signs of:
- Wear: weakened or twisted frames.
- Loose rungs or hardware.
- Worn out anti-slip plastic or rubber shoes.
This inspection is required regardless of the type of ladder you are working with.
Viewing CSA Standards as Referenced in NB Legislation
Certain CSA standards are available for online viewing or purchase from the CSA Group.
To access these, you must first create an account with CSA Communities
Once you are logged in, click on the "OHS Standards / View Access" option.
Click on New Brunswick to see the CSA Standards as referenced in N.B. legislation.
General Regulation - Occupational Health and Safety
Act
N.B. Reg. 91-191
Part X CONSTRUCTION, TRAFFIC AND BUILDING SAFETY
Section 121 Fixed Ladders
121. (1) An employer shall ensure that a fixed ladder
(a) is of adequate strength and length,
(b) is clean and free from grease,
(c) is maintained in a safe condition,
(d) is securely held in place at the top and bottom and at such intermediate points as are required to prevent sway,
(e) has a clearance of at least 165 mm maintained between the rungs and the structure to which the ladder is affixed,
(f) does not have any rungs that extend above a landing,
(f.1) is placed in such a way that an adequate landing surface that is clear of obstructions is available at the top and bottom of the ladder for access and egress,
(g) has side rails or other secure hand holds that extend at least 1.07 m above the landing and are spaced not less than 685 mm apart, and
(h) is removed from service when it has loose, broken or missing rungs, split side rails or other defects that may be hazardous to an employee.
(2) An employer shall ensure that a fixed ladder that is more than 6 m in height is equipped with ladder cages.
(3) Subsection (2) does not apply where an employee on the ladder uses a fall-arresting system.
(4) Where a ladder cage is used on a fixed ladder, an employer shall ensure that
(a) the cage is provided with metal hoops spaced to prevent an employee from falling away from the ladder and to contain an employee who may lean or fall against the cage,
(b) the cage extends not less than 685 mm and not more than 725 mm from the centre line of the rungs of the ladder,
(c) the cage is not less than 685 mm wide where it attaches to the ladder,
(d) the cage extends from a point 2.5 m from the base of the ladder to the top of the ladder,
(e) the inside of the cage is free of projections, and
(f) if the fixed ladder is more than 9 m in height, it is equipped with a rest platform at intervals of no more than 9 m.
[N.B. Reg. 96-106, s. 6; 2010-159, s. 22; 2024-38, s. 60]
Demolition
Part XI TEMPORARY STRUCTURES
Section 122
122. (1) An employer shall ensure that a portable ladder used at a place of employment is
(a) of adequate strength and length,
(b) clean and free of grease, and
(c) maintained in a safe condition.
(2) An employer shall ensure that a portable ladder is removed from service when it has loose, broken or missing rungs, split side rails or other defects that may be hazardous to the safety of an employee.
[N.B. Reg. 2024-38, s. 62]
Section 123
123. An employer shall ensure that a wooden portable ladder
(a) is made of No. 1 grade or better spruce or fir,
(b) is not painted other than by being preserved with a transparent protective coating,
(c) if a single ladder, does not exceed 6 m in length,
(d) has rungs
(i) free of knots,
(ii) designed to carry a load of 200 kg placed at the centre,
(iii) uniformly spaced with a maximum rise of 300 mm,
(iv) secured to each side of the side rail of the ladder by at least three screws or barbed nails of adequate length or by attachments giving equivalent or better strength, and
(v) notched into the side rails of the ladder at least 13 mm on the lower side or with fillers installed between the rungs, and
(e) has side rails
(i) dressed on all sides and without sharp edges, and
(ii) with a uniform clear width between them of not less than 300 mm for ladders 3 m in length or less, and increasing 1 mm in width for each 100 mm in excess of 3 m.
Section 124 Portable Ladders
124. (1) An employer shall ensure that a portable ladder complies with and is used in accordance with either of the following standards:
(a) CSA standard Z11-12 (R2017), Portable ladders or a standard offering equivalent or better protection; or
(b) ANSI standard ANSI ASC A-14.7-2011, Safety Requirements for Mobile Ladder Stands and Mobile Ladder Stand Platforms or a standard offering equivalent or better protection.
(2) An employer shall ensure that a portable extension ladder
(a) has no more than three sections,
(b) has locks that securely hold the sections of the ladder in an extended position, and
(c) when extended, maintains a minimum overlap as follows:
(i) where the ladder is 11 m or less, the overlap shall be 1 m;
(ii) where the ladder exceeds 11 m and is 15 m or less, the overlap shall be 1.25 m; and
(iii) where the ladder exceeds 15 m and is 22 m or less, the overlap shall be 1.5 m.
(3) An employee working 3 m or more above the ground or floor level on a portable ladder may work without a fall-protection system if
(a) the work is a light duty task of short duration at each location,
(b) the employee's centre of gravity is maintained between the two ladder side rails,
(c) the employee will generally have one hand available to hold on to the ladder or another support, and
(d) the ladder is not positioned near an edge or floor opening that would significantly increase the potential fall distance.
[N.B. Reg. 2010-159, s. 23; 2024-38, s. 63]
Section 125
125. (1) An employee who uses a portable ladder shall
(a) inspect the ladder before use,
(b) report any unsafe condition of the ladder to the employer,
(c) face the ladder and use both hands when climbing or descending, and
(d) when standing on a ladder, stand in the centre between the side rails.
(2) An employee who uses a portable ladder shall ensure that
(a) the ladder is secured against movement,
(b) the side rails of the ladder extend at least 1 m above any platform or landing to which the ladder is a means of access, and
(c) if a step ladder, the legs are securely held in position by means of metal braces or an equivalent rigid support.
(3) An employee who uses a portable ladder shall not
(a) splice ladders together unless the spliced section is braced so that the spliced side rails are as strong as the original side rails,
(b) place a ladder in front of or against a door unless the door is blocked in the open position, locked or guarded,
(c) use a ladder as scaffold flooring or as support for scaffold flooring,
(d) stand on the material shelf, the top or the top step of a portable step ladder, or
(e) work from the top three rungs of a portable single or extension ladder.
(4) Paragraphs (1)(d) and (3)(c) and (e) do not apply to a firefighter engaged in structural fire-fighting or rescue.
[N.B. Reg. 97-121, s. 22]
Part XIX ELECTRICAL SAFETY
Section 286
286. In this Part
"electrical equipment" means any wiring, apparatus, instrument, fitting, fixture, machinery or device that transforms, transmits, distributes, supplies or utilizes electricity, but does not include energized electrical utility lines or utility line equipment or household appliances;
"electrical hazard" means a danger of electric shock, arc flash burn, thermal burn or arc blast injury resulting from contact with electrical equipment or failure of that equipment;
"electrically safe work condition" means, with respect to electrical equipment that operates at 30 VAC or 60 VDC or more, a state in which an electrical conductor or a circuit part has been disconnected from energized parts of the electrical equipment, locked out, tested to ensure the absence of voltage and, if necessary, grounded;
"energized", when applied to electrical equipment, means electrically connected to or a source of voltage;
"qualified person" means
(a) when applied to work on electrical equipment, a person who meets the requirements of section 11 or 24 of New Brunswick Regulation 84-165 under the Electrical Installation and Inspection Act;
(b) when applied to work on an energized electrical utility line or utility line equipment,
(i) a person who holds a certificate of qualification issued under the Apprenticeship and Occupational Certification Act for the distribution construction lineman trade, the powerline technician trade or the power system technician trade, or
(ii) a person who is registered as an apprentice under the Apprenticeship and Occupational Certification Act for an occupation described in subparagraph (i) and who is working under the supervision of a person described in subparagraph (i),
(c) when applied to work in an arboricultural operation described in section 369 that occurs closer to an energized electrical utility line or utility line equipment than the distances set out in subsection 289(1), an employee who meets the requirements of section 369,
(d) when applied to any other type of work that occurs closer to an energized electrical utility line or utility line equipment than a distance set out in subsection 289(1), an employee who is trained to use and follows a code of practice established by the employer, and
(e) when applied to work referred to in paragraph (a), a person who is
(i) knowledgeable about the provisions of this Act and the regulations that apply to the assigned work, and
(ii) knowledgeable about the actual and potential dangers to health and safety associated with the assigned work.
[N.B. Reg. 2001-33, s. 94; 2022-79, s. 82]
Section 289 Utility Lines and Utility Line Equipment
289. (1) An employer shall ensure that an employee who is not a qualified person does not carry out any work, and no such employee shall carry out any work, that is liable to bring any person or object closer to an energized electrical utility line or utility line equipment than the distances specified in the following table:
Table
Phase to Phase Voltage of Energized Electrical Utility Line or Utility Line Equipment | Distance |
Up to 750 v | 900 mm |
750 v - 100,000 v | 3.6 m |
100,001 v - 250,000 v | 5.2 m |
250,001 v - 345,000 v | 6.1 m |
(2) Where an employee who is not a qualified person is about to commence work that is liable to bring any person or object closer to an energized electrical utility line or utility line equipment than a distance specified in subsection (1), an employer shall contact the authority owning or operating the energized electrical utility line or utility line equipment and shall ensure that the utility line or utility line equipment
(a) is de-energized, or
(b) is adequately insulated or guarded
before permitting the employee to commence the work.
[N.B. Reg. 2001-33, s. 100]