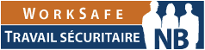
Lockout
Correct lockout prevents serious injuries caused by the unexpected start-up or release of energy or hazardous substances when machines are being serviced or maintained.
There are four necessary actions in any lockout procedure:
- Identify all energy sources connected with your work.
- Disable, redirect, or stop all energy from becoming active during the repair or replacement.
- Apply restraint devices to prevent the system from starting up while you work on it.
- Confirm that you have reached a zero energy state by doing a restart or bump test.
[Ref. WorkSafe NB, Safety Talk-Lock out]
As an employer, you must:
- Establish a written lockout procedure for each and every machine for when it is cleaned, maintained, adjusted or repaired.
- Ensure the energy source to a machine can be isolated and locked, is in a location familiar to all employees, and is properly identified.
- Provide safety locks and keys needed to lock out machines.
- Train employees who need to lock out the machine on the procedure.
- Ensure no one works on a machine until all the energy sources are locked out and it is placed in a zero energy state by a competent person.
- Make sure ALL employees who are working on the machine verify:
- All energy sources are turned off
- The machine is locked out with lock and key
- Tags are placed on the lock and include directions to not start the machine, the employee's name and signature, and the date and time when the tag was placed.
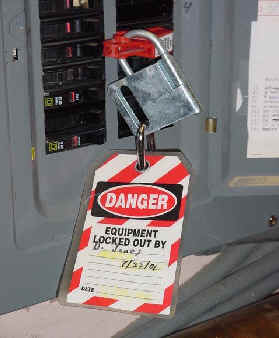
- Confirm that all employees understand that no person is to remove a lock or tag except for the person who installed it, or in an emergency, a competent employee designated by the employer.
- Where a lockout procedure is not appropriate or inadequate, the employer must establish and enforce a code of practice in consultation with the joint health and safety committee or health and safety representative.
While the employer is ultimately responsible for all the provisions mentioned above, the supervisor has a vital role to play in the safety of their teams. As a supervisor, you must:
- Acquaint your employees with the hazards and control measures associated with their work
- Provide the information and instruction necessary to ensure their health and safety
- Enforce company safety rules, programs, codes of practice and procedures, including ensuring employees comply with the requirements below.
As an employee, you must:
- Be trained and authorized by your employer to use a lockout procedure.
- Always follow the written lockout procedure (or code of practice) for each machine established by your employer and not take any shortcuts.
- Use only the locks and tags specified and provided by your employer.
- Secure your lock and tag it when a multiple lock device (scissor clamp), chain, or block is used on a machine.
- Only work on a machine after someone competent verifies the machine is in a zero energy state and locked out and tested.
- Understand that locks are your personal security devices that can only be removed by the person who controls the lock (you).
- Clear the work area before reactivating the machine or equipment.
When you put your multiple lock device (scissor clamp), chain, or block on a piece of equipment, you also have to lock and tag it. [Reference: WorkSafe NB, Safety Talk-Lock out]
Ensure the equipment is disconnected from the energy source(s) by first checking that no personnel are exposed. Then verify the isolation of the equipment by operating the push buttons or other normal operating control(s), or by testing to make certain the equipment will not operate. CAUTION: return operating control(s) to neutral or “OFF” position after verifying the isolation of the equipment.
“competent” means
- (a) qualified, because of such factors as knowledge, training and experience, to do assigned work in a manner that will ensure the health and safety of persons,
- (b) knowledgeable about the provisions of the Act and the regulations that apply to the assigned work, and
- (c) knowledgeable about potential or actual danger to health or safety connected with the assigned work
The tag indicates who locked out the machine, it directs people not to start or operate the machine, and it notes when the lock was applied.
50.2(4) The code of practice shall include the following:
(a) possible hazardous situations, including a description of the hazards and the possible effects on the health or safety of employees;
(b) the identification of employees at risk;
(c) the location where the code of practice might apply;
(d) the methods and equipment to be used including inspections procedures;
(e) the procedures and equipment which might be required in the event of an emergency;
(f) the times, days, or events during which the code of practice might be applicable;
(g) the identification of training needs;
(h) the identification of the person responsible for implementing the code of practice; and
(i) the name of the safety monitor, if applicable, and the training the safety monitor has received
General Regulation - Occupational Health and Safety
Act
N.B. Reg. 91-191
Part XVI MECHANICAL SAFETY
Section 239 Lock out
239. (1) An employer shall ensure that in addition to the normal control start and stop mechanism, any equipment or machine has a means of isolating the energy source to the equipment or the machine that is
(a) lockable,
(b) in a location familiar to all employees, and
(c) properly identified.
(2) An employer shall provide a safety lock and key to an employee who may have to lock out any equipment or machine.
(3) An employer shall establish a written lock out procedure for equipment and machines and ensure that an employee who may be required to lock out the equipment or the machine is adequately instructed and trained to lock out the equipment or the machine.
(4) Subject to section 240, where any equipment or machine is to be cleaned, maintained, adjusted or repaired, an employer shall ensure that no employee works on the equipment or the machine until
(a) a competent person puts the equipment or the machine in a zero energy state,
(b) each employee who will be working on the equipment or the machine
(i) verifies that all potential energy sources have been made inoperative,
(ii) locks out the equipment or the machine using the safety lock and key provided by the employer, and
(iii) puts a non-conductive tag on the safety lock that contains
(A) words directing persons not to start or operate the equipment or machine,
(B) the qualified person’s printed name and signature, and
(C) the date and time when the tag was put on the safety lock.
(5) No employee shall clean, maintain, adjust or repair any equipment or machine until the employee verifies that paragraphs (4)(a) and (b) have been complied with and verifies by testing that the equipment or the machine is inoperative.
(6) No person shall remove a safety lock or tag except
(a) the person who installed it, or
(b) in an emergency or where attempts made to contact the person referred to in paragraph (a) indicate the person is not available, a competent employee designated by the employer.
[N.B. Reg. 2001-33, s. 86; 2022-79, s. 50]
Section 240
240. Where the lock out procedure referred to in section 239 is inappropriate for the cleaning, maintenance, adjustments or repairs to be performed or is inadequate for the protection of an employee, an employer shall
(a) establish a code of practice in consultation with the committee or health and safety representative, if any, specifying personnel responsibilities, personnel training and details of procedure for the neutralization, clearance, release and start up of the equipment or machine, and
(b) comply with and enforce the code of practice.
[N.B. Reg. 2001-33, s. 87; 2022-27, s. 36; 2022-79, s. 51]