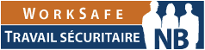
Manual Material Handling
Manual material handling (MMH) is the most common cause of occupational fatigue and lower back pain. MMH includes any tasks that require a person to lift, lower, push, pull, hold or carry any object or material.
Be aware that handling hazardous material (asbestos, chemicals, etc.) will have requirements listed in other sections of the OHS Act and regulations.
As an employer, you must:
- Ensure that materials, machines or equipment are stored and located so they do not create a hazard to an employee.
- Provide the necessary equipment to the employee for lifting and moving an object or material, and ensure the equipment is used by the employee.
- Instruct employees on the appropriate method of lifting and moving objects and material, including how to use the equipment provided.
Handling Heavy Objects
Handling and moving heavy objects requires special precautions. As the employer, you must ensure employees handling heavy objects:
- Have and use chocks and ropes or other tackle to control the motion of the object.
- Have and use bars or sledges to change the direction of moving rollers.
- Do not stand on the downward side of an incline when moving heavy objects.
The guideline Developing a Code of Practice for Manual Handling can be used to develop safe practices and prevent injuries related to manual material handling. Key steps in preventing injuries from manual material handling include:
- Identifying high-risk manual handling tasks that involve heavy physical exertion, have a high score on the discomfort survey, or have resulted in a musculoskeletal injury in the past.
- Assessing the tasks using the checklist. Consider the following risk factors:
- Forceful exertion (weight of objects, pushing/pulling force, carrying distance)
- Awkward posture (angle of body joints, workstation dimensions, working height)
- Repetitive motion (number of repetitions, duration, production rate)
- Identifying solutions to reduce or eliminate the risk factors.
- Regularly evaluating the tasks being performed, including investigating reported incidents due to manual handling and following up on employee concerns.
Consider solutions such as:
- Changing the design of the job itself (work and rest schedules, job rotation, production rate).
- The object being handled (weight, size, shape, handle).
- The workstation (dimensions, layout, adjustability).
- Providing mechanical aid.
- Lifting, using employee teams.
- Employee education, such as:
- Understanding the principles of body mechanics
- Recognizing high-risk tasks
- Reporting symptoms and incidents early so that necessary action can be taken
- Performing warm-up stretches and exercises
Any one solution may not eliminate all the risks of injury. Choose the solution that best applies to your situation and use it as a starting point to improve your work environment.
While the employer is ultimately responsible for all the provisions mentioned above, the supervisor has a vital role to play in the safety of their teams. As a supervisor, you must:
- Acquaint your employees with the hazards and control measures associated with their work
- Provide the information and instruction necessary to ensure their health and safety
- Enforce company safety rules, programs, codes of practice and procedures.
General Regulation - Occupational Health and Safety
Act
N.B. Reg. 91-191
Part II SANITATION AND ACCOMMODATION
Section 16 Storage of items not to create hazard
16. An employer shall ensure that materials, machines or equipment are not stored or located in a place of employment so as to create a hazard to an employee.
Part VIII HANDLING AND STORAGE OF MATERIALS
Section 52 General Handling of Objects and Material
52. Where the health or safety of an employee handling an object or material may be endangered, an employer shall ensure that
(a) adequate and appropriate equipment is provided to the employee and is used by the employee for lifting and moving the object or material, and
(b) the employee is instructed as to the appropriate method of lifting and moving objects and material.
Section 53 Heavy Objects
53. (1) Where a heavy object is handled on an incline, an employer shall ensure that an employee handling the object uses, and the employee handling the object shall use, chocks and ropes or other tackle to control the motion of the object, and both shall ensure that other employees do not stand on the downward side of the incline.
(2) Where a heavy object is moved by using rollers, an employer shall ensure that an employee moving the object uses, and the employee moving the object shall use, bars or sledges to change the direction of the moving rollers.