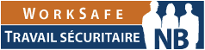
Propane (Compressed)
In the construction industry, propane is used in various applications: fuel in tar pots, welding torches, heaters, appliances and some forklift engines. Compressed gas cylinders filled with propane gas should be handled, used and stored with proper care to prevent leaks and explosions.
Propane is a hazardous product under WHMIS. It is also heavier than air, and in the event of a leak it can accumulate in low-lying areas such as basements, pits and trenches. Propane gas is colourless and odourless, but suppliers add an odorant to the gas so that leaks can be detected by smell. The smell is similar to rotten cabbage or rotten egg.
The release of propane gas into a confined area or an area with poor ventilation can displace the oxygen content in the air and cause asphyxiation.
As an employer, you must:
- Use the information on safety data sheets, supplier specifications, and the safe handling rules in the standard CGA G-P-1-1991, "Safe Handling of Compressed Gases in Containers" to ensure that compressed gas containers are used, stored and handled safely.
- Store compressed gas cylinders:
- In a well-ventilated and dry storage area where temperatures are below 52°C.
- Upright and secured with a rope, wire or chain to prevent falling during transportation, usage or storage.
- Separately, away from processing and handling areas, and from incompatible materials (do not store with oxidizing agents, oxygen or chlorine. Review the SDS); separate storage can minimize personal injury and damage in case of fires, spills or leaks.
- In a storage area that is well labelled with the names of the gases stored, and signs indicating no smoking.
- So that full containers and empty containers are stored separately.
- Cylinders must be inspected and re-qualified every 10 years by an organization certified by Transport Canada (https://propane.ca/safety/).
- Ensure compressed gas cylinders are kept where they will not be struck by falling materials or moving equipment, and at a safe distance from ignition or heat.
- Close all valves when cylinders are not in use except when gas is flowing from the container, the gas in the container is maintaining pressure in a supply line, or the container is on stand-by during and between operations using the gas.
- Never drag, slide or allow cylinders to be handled roughly.
- Never lift cylinders with magnets, chains or wire rope slings. Use a hoisting cradle to lift or lower cylinders from one level to another.
- Never transport compressed gas containers in the trunk of a car or in a closed van.
- Avoid skin contact with the gas as it is extremely cold and can cause frostbite.
- Educate employees to recognize the smell and know how to respond if there is a leak.
- Conduct regular inspection of cylinders and equipment to provide a warning of potential hazards:
- Examine regulators, pressure relief valves and cylinder connections.
- Ensure that cylinders are free of corrosion, leakage, pitting, dents or gouges.
Since propane is a controlled product, pertinent WHMIS regulation will have to be followed. The OHS Guide topic on WHMIS tells suppliers, employers and employees how to work safely with propane.
Employees working close to or with propane must be:
- Informed of all the hazard information received from the supplier, as well as any further information of which the employer is aware or ought to be aware;
- Instructed and trained in the content required on a supplier label and on a safety data sheet;
- Informed of procedures for the safe use, storage, handling and disposal of a controlled product and in the event of an emergency.
A safety data sheet for propane must be obtained by the employer and made available to employees and the JHSC.
While the employer is ultimately responsible for all the provisions mentioned above, the supervisor has a vital role to play in the safety of their teams. As a supervisor, you must:
- Acquaint your employees with the hazards and control measures associated with their work
- Provide the information and instruction necessary to ensure their health and safety
- Enforce company safety rules, programs, codes of practice and procedures, including ensuring employees comply with the requirements below.
Additional Information
When using propane, there is a risk of poisoning with carbon monoxide (CO), which is a colourless, odourless and tasteless gas. This risk increases when the equipment is not installed, used, maintained properly or with insufficient ventilation.
Employees must be instructed to recognize the symptoms of CO poisoning. The first signs of CO exposure are headache and fatigue. Increased exposure can rapidly lead to loss of consciousness, arrested breathing, heart failure and death.
How to identify and take preventive actions when there is a propane leak:
- Propane leaks smell like rotten eggs or rotten cabbage.
- If you smell propane, if possible, shut the source of the leak and evacuate the premises immediately. Follow up with the fire department and propane supplier.
- Avoid touching electrical switches or appliances when a leak is suspected.
- Inform employees of the dangers of resetting a breaker inside a control panel. Only allow qualified persons to reset a breaker if live parts are exposed.
- Do not allow anyone to operate any equipment or something as simple as turning on a light switch.
- Any modification or addition to existing gas installations must be done by a certified technician.
- Don't return until the area has been thoroughly ventilated to remove the gas.
- Never enter the area without somebody standing by to help in case you run into trouble.
- Don't let propane saturate your clothing. Clothing remains highly flammable for some time after exposure. Even if it doesn't feel or smell unusual, clothing soaked in propane should be removed and aired outside.
- Install a certified by the CSA Group or Underwriters Laboratories of Canada (ULC) carbon monoxide detector.
“asphyxiation” means loss of consciousness and suffocation or death because of insufficient oxygen to breathe.
General Regulation - Occupational Health and Safety
Act
N.B. Reg. 91-191
Part VIII HANDLING AND STORAGE OF MATERIALS
Section 75
75. (1) An employer shall ensure that a portable compressed gas container is used, stored and handled so as not to endanger an employee's health or safety.
(2) In complying with subsection (1), an employer shall use as a guide
(a) information on a safety data sheet,
(b) the specifications provided by the supplier, and
(c) the safe handling rules in CGA standard P-1-2008, Safe Handling of Compressed Gases in Containers - 11th Edition or a standard offering equivalent or better protection.
(3) Repealed. [N.B. Reg. 2022-79, s. 14]
[N.B. Reg. 2001-33, ss. 25, 26; 2016-7, s. 2; 2022-79, s. 14; 2024-38, s. 50]
Section 76
76. (1) An employer shall ensure that a portable compressed gas container is stored
(a) in a well ventilated and dry storage area where the temperature does not exceed 52°C,
(b) with containers grouped by types of gas and the groups arranged to take into account the gases contained,
(c) with full and empty containers in separate areas, and
(d) secure and upright.
(2) An employer and an employee shall each ensure that a portable compressed gas container
(a) is not stored near readily ignitable substances,
(b) is kept at a safe distance from all operations that produce flames, sparks or molten metal or result in excessive heating of the container,
(c) is not exposed to corrosive materials or corrosion-aiding substances, and
(d) is protected from falling and from having heavy objects fall on it.
(3) An employer shall ensure that a storage area for portable compressed gas containers is prominently posted with the name of the gases stored and with signs prohibiting smoking.
Section 77
77. (1) An employer shall ensure that a portable compressed gas container is not
(a) rolled on its side, dragged, slid or subjected to rough handling, or
(b) moved by a lifting magnet.
(2) Where appropriate lifting mechanisms have not been provided on a portable compressed gas container, an employer shall ensure that suitable cradles or platforms for holding the container are used for lifting.
Section 78
78. (1) An employer and an employee shall each ensure that regulators, automatic reducing valves, gauges, hoses and other appliances provided for use with a particular gas or group of gases are not used on a portable compressed gas container containing a gas having different chemical properties unless information obtained from the supplier of the portable compressed gas container states that this can be safely done.
(2) An employer shall ensure that
(a) connections on a portable compressed gas container to piping, regulators and other appliances are kept tight to prevent leakage,
(b) connections to a portable compressed gas container that do not fit are not forced,
(c) the valves on a portable compressed gas container are kept closed at all times whether the container is charged or empty, except when
(i) gas is flowing from the container,
(ii) the gas in the container is maintaining pressure in a supply line, or
(iii) the container is on stand-by during and between operations using the gas,
(d) check valves and flashback arrestors for a portable compressed gas container are installed as close as possible to fuel gas and oxygen regulators, and
(e) CSA standard W117.2-12 (R2017), Safety in welding, cutting, and allied processes or a standard offering equivalent or better protection is used as a guide to determine the best location for check valves and flashback arresters.
[N.B. Reg. 2024-38, s. 51]
Workplace Hazardous Materials Information System Regulation - Occupational Health
and Safety Act
N.B. Reg. 2016-6
EMPLOYEE EDUCATION, INSTRUCTION AND TRAINING
Section 6 Hazard information
6. (1) An employer shall ensure that an employee who works with a hazardous product or who may be exposed to a hazardous product in the course of his or her work activities is informed of all hazard information received from a supplier concerning the hazardous product, as well as any further hazard information concerning the hazardous product of which the employer is aware or ought to be aware concerning the use, storage and handling of the hazardous product.
(2) If a hazardous product is produced at a place of employment, an employer shall ensure that an employee who works with the hazardous product or who may be exposed to the hazardous product in the course of his or her work activities is informed of all hazard information of which the employer is aware or ought to be aware concerning the hazardous product.
Section 7 Program of employee education, instruction and training
7. (1) An employer shall ensure that an employee who works with a hazardous product or who may be exposed to a hazardous product in the course of his or her work activities receives education, instruction and training in
(a) the content required on a supplier label and workplace label and the purpose and significance of the information contained on the labels,
(b) the content required on a safety data sheet and the purpose and significance of the information contained on the safety data sheet,
(c) procedures for the safe use, storage, handling and disposal of a hazardous product,
(d) specific information needed for the safe use, storage, handling and disposal of a hazardous product contained or transferred in
(i) a pipe,
(ii) a piping system including valves,
(iii) a process vessel,
(iv) a reaction vessel, or
(v) a tank car, tank truck, ore car, conveyor belt or similar conveyance,
(e) procedures to be followed where fugitive emissions are present and where employees may be exposed to the fugitive emissions, and
(f) procedures to be followed in case of an emergency involving a hazardous product.
(2) An employer shall ensure that the program of employee education, instruction and training required by subsection (1) is
(a) developed and implemented for the employer’s place of employment,
(b) related to any other hazard prevention and control program at the place of employment, and
(c) developed and implemented in consultation with the committee, if any, or the health and safety representative, if any.
(3) So far as is reasonably practicable, an employer shall ensure that
(a) the program of employee education, instruction and training required by subsection (1) results in an employee being able to apply the information as needed to protect the employee’s health and safety,
(b) the knowledge of the employees is periodically evaluated using a written test, practical demonstration or other suitable means, and
(c) the requirements of paragraph (b) are determined in consultation with the committee, if any, or the health and safety representative, if any.
(4) An employer shall review at least annually, or more frequently if required by a change in work conditions or available hazard information, and in consultation with the committee, if any, or health and safety representative, if any, the education, instruction and training provided to employees concerning hazardous products.
SAFETY DATA SHEETS
Section 14 Supplier safety data sheets
14. (1) Subject to subsection (2), an employer who acquires a hazardous product for use, handling or storage at a place of employment shall obtain a supplier safety data sheet in respect of that hazardous product that complies with the requirements of the Hazardous Products Regulations .
(2) If a supplier is exempted by the Hazardous Products Regulations from the requirement to provide a safety data sheet for a hazardous product, the employer is exempt from the requirement to obtain and provide a safety data sheet for that hazardous product.
(3) If an employer is unable to obtain an up-to-date supplier safety data sheet referred to in subsection (1), the employer shall add any significant new data applicable to the hazardous product to the most recent supplier safety data sheet obtained under that subsection on the basis of the ingredients of the hazardous product disclosed in that supplier safety data sheet.
(4) An employer may provide a safety data sheet in a format different from the format in the supplier safety data sheet or containing additional hazard information if
(a) it discloses no less information than that disclosed on the supplier safety data sheet,
(b) it indicates that the supplier safety data sheet is available, and
(c) the employer makes the supplier safety data sheet readily available.
(5) If a hazardous product is received at a laboratory from a laboratory supply house or is a laboratory sample and the supplier has provided a safety data sheet, an employer shall ensure that a copy of the safety data sheet is made available to employees in the laboratory.
Section 16 Availability of safety data sheets
16. An employer shall ensure that
(a) a copy of a safety data sheet referred to in sections 14 and 15 is readily available to employees who may be exposed to the hazardous product and to the committee, if any, or to a health and safety representative, if any, and
(b) the committee, if any, or a health and safety representative, if any, is consulted on the means to best achieve safety data sheet accessibility in the place of employment.