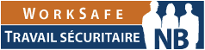
Safeguards
Machines with moving parts and machines that could potentially send objects flying in the event of failure are dangerous and employers and employees must take proper precautions. Physical contact with or objects thrown from machines are responsible for serious injuries and death. Although safeguarding is not the only tool available to prevent incidents, it's an important one, and required by law.
Hazards associated with machinery include contact with:
- Moving parts
- Flying objects (fragment from an abrasive wheel)
- Electricity
- Heat or cold
- Gas or liquid under pressure
- Materials, chemicals or other substances
Common injuries from working with and around machinery include crushing, amputations, burns, lacerations and electric shock. This document only provides guidance on preventing injuries associated with contact with moving machinery or machine parts.
The main machine movements that can cause injuries include:
- Rotation – rotating parts of the machine creates nip points that can grip clothing, jewelry, appendages (hands, arms, feet, and legs), hair and other dangling objects. The item that is gripped can be dragged into the machine, causing further damage or severe injury. A lathe is an example of this type of machine.
- Sliding - motions that involve the movement of one part along a stationary part, or the movement of one part over another part that is moving in the opposite direction of the first part. These types of motions can entrap, cut, crush, or strike an individual. An example of this type of machine is a four-slide metal working machine.
- Shearing - motions involve the application of a force on an object perpendicular to its surface. If a force is applied perpendicularly, in two opposing directions at the same time, and in the same place on an object, the object will be cut (a similar action is cutting with scissors). An example of this type of machine is a die cutting machine.
- Crushing - occurs as a result of at least two objects moving in opposing directions toward one another, or one object moving toward a stationary object. An example of this type of machine is a mechanical break press.
- Punching - motions are used to create indentations or holes in materials. It typically involves the perpendicular movement of a small item onto the surface of a material. Both crush and shear injuries can also occur at these points of contact. An example of this type of machine is a punch press.
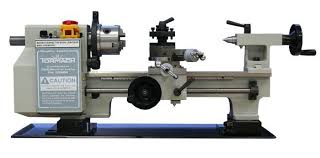
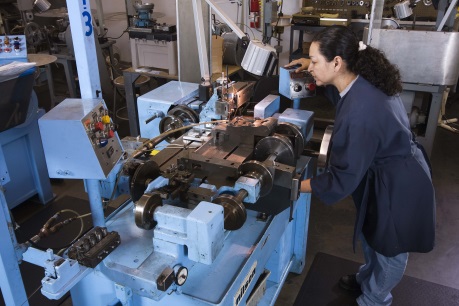
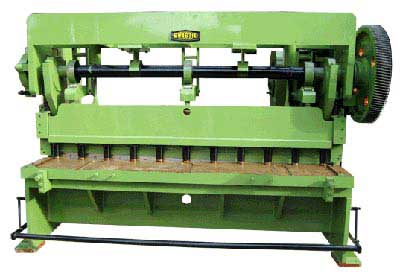
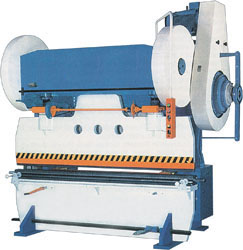
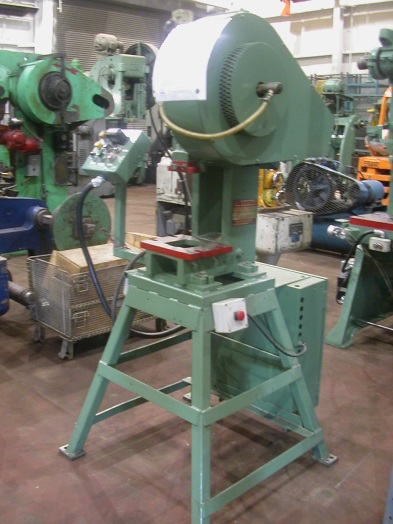
To protect employees from coming into contact with these movements and other harmful conditions, safeguards need to be in place or other controls must be taken. Safeguards can be in the form of:
- Barrier guards - physically prevent an employee from reaching around, over, under, and through the guard to the danger area. Fixed barrier guards are used when access to the danger area is not required during normal operation. When accessing the danger area during production, the barrier guard can be interlocked with the machine's control system. This interlock prevents the machine from moving while the guard is removed.
- Safeguarding devices - are designed to allow employees access to a danger zone, without having to remove physical guarding. These devices do not allow the machine to start operating, or they stop the machine from operating while an employee or part of an employee is in the danger zone. These types of controls include:
- Presence-sensing devices - light curtains, pressure sensitive mats, and photoelectric devices.
- Alternative operating modes - limit the machine movement or travel at a safe range or speed. This option is ideal for machine set-ups or die changes.
- Emergency stop devices - sense when an operator is or has entered the danger zone and immediately stops the machine cycle.
- Placement of Controls - by placing controls in locations away from the danger zone, the employee is protected while the machine is operating. Controls that fall in this category include the “hold-to-run control”, “deadman”, or, “operator-maintained” control.
- Location - Control by location involves designing the machine so access to the machine's danger zones (moving parts) is eliminated during normal operation. Keep methods of access to the machine such as walkways, access platforms, or service ladders at a specific distance from the danger zone.
- Administrative controls - Control through training, supervision and procedures, including lockout procedures.
[Reference: WorkSafeBC: Safeguarding Machinery and Equipment: General Requirements]
As an employer, you must:
- Ensure machines are erected, installed, assembled, started, operated, used, handled, stored, stopped, serviced, tested, cleaned, adjusted, maintained, repaired and dismantled in accordance with the manufacturer's specifications.
- Ensure that the manufacturer's rated capacity or other limitation of operations of the machine are not exceeded.
- Regularly inspect for defective machines and remove from service until repaired.
- Guard any pedal that is used to activate a control device on a machine.
- Provide sufficient space around a machine when it is in operation or when employees do the cleaning, maintenance, adjustments, or repairs.
- Provide adequate safeguards to protect employees from contacting moving parts of the machinery except when the machine is equipped with a device that stops the machine automatically before an employee comes into contact with a moving part.
- Provide a safeguard strong enough to contain or deflect any flying object.
- Ensure that a safeguard that interlocks with the machinery controls is not altered to prevent its operation.
- Physically modify the machine when it has been determined that an adequate safeguard is not possible, or develop a safe work procedure to protect employees.
- Never allow anyone to remove or render ineffective a safeguard for a machine unless it is necessary to enable cleaning, maintenance, adjustment or repair.
- Ensure that an abrasive wheel is checked for flaws before being installed, fitted with a protective hood of sufficient strength, and mounted in accordance with the manufacturer's specifications.
- Use abrasive wheels as recommended by the manufacturer's specifications.
- Ensure gears and sprockets are completely enclosed or enclosed on exposed sides if there is a hazard from exposed spokes.
- Guard with casting that completely encloses the shaft any exposed parts of a permanently installed shaft that is within 2.1 m of an access point.
- Guard with a non-rotating cap or safety sleeve any shaft ends that project more than half their diameter.
While the employer is ultimately responsible for all the provisions mentioned above, the supervisor has a vital role to play in the safety of their teams. As a supervisor, you must:
- Acquaint your employees with the hazards and control measures associated with their work
- Provide the information and instruction necessary to ensure their health and safety
- Enforce company safety rules, programs, codes of practice and procedures, including ensuring employees comply with the requirements below.
As an employee, you must:
- Wear close fitting clothing, confine or cut head and facial hair, and not wear jewellery, rings, dangling neckwear or similar items around moving machinery parts.
- Not exceed the manufacturer's rated capacity or other limitations of the machine.
- Never remove or render ineffective a safeguard for a machine unless it is necessary to enable cleaning, maintenance, adjustment or repair.
- When you remove or render ineffective a safeguard, replace the safeguard and ensure it is functioning properly before leaving the machine.
- Put the machine in a zero energy state and lockout or follow the code of practice before removing or rendering ineffective the safeguard if you cannot directly control the machine.
- Never operate abrasive wheels at a speed exceeding the manufacturer's specifications.
- Not grind on the side of an abrasive wheel unless the wheel is designed for that purpose.
- Not adjust a tool rest while an abrasive wheel is in motion.
- Report to the employer or supervisor any safeguarding hazards.
“safeguard” means a guard, shield, guardrail, fence, gate, barrier, safety net, wire mesh or other protective enclosure, handrail or other similar device designed to protect the safety of a person, but does not include protective equipment.
“moving parts” – means drive or idler belts, rollers, gears, driveshafts, keyways, pulleys, sprockets, chains, ropes, spindles, drums, counterweights, flywheels, couplings, pinchpoints, cutting edges or other moving parts.
OCCUPATIONAL HEALTH AND SAFETY ACT
S.N.B. 1983, c. O-0.2
DUTIES OF EMPLOYERS, OWNERS, CONTRACTORS, SUB-CONTRACTORS, SUPERVISORS, EMPLOYEES AND SUPPLIERS
Section 12 Duties of employee
12. Every employee shall
(a) comply with this Act, the regulations and any order made in accordance with this Act or the regulations;
(b) conduct themselves to ensure their own health and safety and that of other persons at, in or near the employee’s place of employment;
(c) report to the employer or supervisor the existence of any hazard of which the employee is aware;
(d) wear or use such protective equipment as is required by regulation;
(e) consult and co-operate with the committee where one has been established or with the health and safety representative where one has been elected or designated; and
(f) co-operate with any person responsible for the enforcement of this Act and the regulations.
[S.N.B. 2001, c. 35, s. 6; 2007, c. 12, s. 3; 2019, c. 38, s. 7; 2022, c. 32, s. 7]
General Regulation - Occupational Health and Safety
Act
N.B. Reg. 91-191
Part XVI MECHANICAL SAFETY
Section 235
235. (1) An employer shall ensure that a machine is erected, installed, assembled, started, operated, used, handled, stored, stopped, serviced, tested, cleaned, adjusted, maintained, repaired and dismantled in accordance with the manufacturer's specifications.
(2) An employer shall ensure that the manufacturer's rated capacity or other limitations on the operation of a machine or any part of it, as set out in the manufacturer's specifications or in any relevant specifications certified by an engineer, are not exceeded.
(3) An operator of a machine shall not exceed the manufacturer's rated capacity or other limitations referred to in subsection (2).
Section 236
236. An employer shall ensure that a machine is regularly inspected for defects and that a defective machine that may cause injury to an employee is removed from service until repaired.
Section 237 Starting and Stopping Machines
237. (1) An employer shall ensure that the operational controls on a machine are
(a) located and protected in such a manner as to prevent unintentional activation, and
(b) suitably identified so as to indicate the nature of each control mechanism.
(2) Where a pedal is used to activate a control device on a machine, an employer shall ensure that the pedal is guarded so that it cannot be struck accidentally and activate the machinery.
(3) An employer shall ensure that each pair of active and idler pulleys on a machine is equipped with a permanent belt shifter that has a mechanical means of preventing the belt from creeping from the idler pulley to the active pulley.
(4) Where there is not a clear view of a machine or parts of it from the control panel or operator's station and moving parts of the machine may endanger an employee when the machine is started, an employer shall ensure that
(a) an alarm system is installed, and
(b) the alarm system gives an effective warning before start-up of the machine so that an employee is made aware of the imminent start-up.
(5) An employer shall ensure that an operator of a machine has unimpeded access in the operator's immediate work area to the means of stopping the machine.
(6) An employer shall ensure that a machine not driven by an individual motor or prime mover is equipped with a clutch, idler pulley or other means of quickly disengaging the power source.
Section 241 Contact with Machines
241. (1) An employer shall ensure that sufficient space is provided around a machine in order to ensure the safety of employees while the machine is being operated or while cleaning, maintenance, adjustments or repairs to the machine are being carried out.
(2) Where an employee or the employee's clothing may come into contact with moving parts of a machine or a moving machine, the employee shall
(a) wear close fitting clothing,
(b) confine or cut head and facial hair, and
(c) not wear jewellery, rings, dangling neckwear or similar items.
Section 242 Safeguards
242. (1) Where an employee may come into contact with moving drive or idler belts, rollers, gears, driveshafts, keyways, pulleys, sprockets, chains, ropes, spindles, drums, counterweights, flywheels, couplings, pinchpoints, cutting edges or other moving parts on a machine that may be hazardous to the employee, an employer shall provide adequate safeguards to prevent such contact.
(2) Subsection (1) does not apply to a machine that is equipped with a device that stops the machine automatically before an employee comes into contact with the parts mentioned in subsection (1).
(3) Where there is a possibility of a failure of a machine that may result in an injury to an employee from a flying object, an employer shall install a safeguard strong enough to contain or deflect any flying object.
(4) No employer or employee shall alter the design of a machine where it has been designed with a safeguard that interlocks with the machinery control so as to prevent the operation of the machine unless the safeguard is in its proper place.
(5) Where an employer has determined that an adequate safeguard for a machine cannot be provided, the employer shall ensure that a physical modification of the machine is carried out or a change in work procedure is put into place to protect employees from being exposed to the hazards associated with the lack of an adequate safeguard.
Section 243
243. (1) No person shall remove or render ineffective a safeguard for a machine unless the removal or rendering ineffective is necessary to enable the cleaning, maintenance, adjustment or repair of the machine.
(2) Where a person removes or renders ineffective a safeguard for a machine, the person shall ensure that the safeguard is replaced and is functioning properly before leaving the machine or that the machine is in a zero energy state.
(3) Where a safeguard for a machine is to be removed or rendered ineffective and the machine cannot be directly controlled by the person who removes or renders ineffective the safeguard, the person shall put the machine in a zero energy state and lock out the machine in accordance with section 239 or follow the code of practice in section 240 before removing or rendering ineffective the safeguard.
[N.B. Reg. 2001-33, s. 88]
Section 244 Abrasive Wheels and Grinders
244. (1) An employer shall ensure that the maximum number of revolutions per minute
(a) of an abrasive wheel, as recommended for safe use in the manufacturer's specifications, is identified on the wheel, and
(b) of a grinder output shaft is identified on the grinder.
(2) An employer shall ensure that an abrasive wheel is
(a) checked for flaws before installation,
(b) fitted with a protective hood of sufficient strength to contain fragments of ruptured wheels, and
(c) mounted in accordance with the manufacturer's specifications.
(3) An employer shall ensure that a tool rest is mounted on a bench grinder as close as is safely possible to the abrasive wheel.
(4) Before applying any work to an abrasive wheel, an employee shall run the wheel at full operating speed in accordance with the manufacturer's specifications.
(5) An employee shall not
(a) operate an abrasive wheel at a speed in excess of the speed set out in the manufacturer's specifications,
(b) do grinding on the side of an abrasive wheel unless the wheel has been designed for that purpose, or
(c) adjust a tool rest while the abrasive wheel is in motion.
Section 249 Gears and Sprockets
249. An employer shall ensure that all gears and chain-drive sprockets
(a) are completely enclosed, or
(b) where complete enclosure is not practicable,
(i) have band-type guards with flanges extending inward beyond the root of the teeth, and
(ii) are enclosed on exposed sides if there is a hazard from exposed spokes.