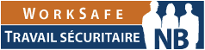
Air Quality
Air quality involves many components, including ventilation, temperature, relative humidity and air contaminants. Control of air quality can be achieved by ventilation systems through the introduction of large quantities of air (dilution ventilation) or the removal of contaminants at the source where they are generated (local exhaust). Ventilation requirements during construction, renovation and building maintenance are also critical in ensuring the health of employees and occupants and may require specialized equipment to mitigate air quality problems.
Note: This section of the regulation does not apply to:
As an employer you must ensure that:
- A work area contains at least 8.5 m3(300 ft3) of air space for each employee who works in that the area.
- When calculating the air space requirement above, heights above 3 m are excluded from the calculation. This requirement means that if a workspace is 2 m wide, 3 m long and 3.5 m in height, the workspace for that employee is calculated as 2x3x3=18m3 and not 2x3x3.5=21 m3.
- A place of employment is adequately ventilated by either:
- If the place of employment is a health care facility, mechanical ventilation that conforms to CSA Z317.2-10, “Special requirements for heating, ventilation and air-conditioning (HVAC) systems in health care facilities” (reaffirmed 2015) or a standard offering equal or better protection.
- Mechanical ventilation that meets the ANSI/ASHRAE standard 62.1-2010, "Ventilation for Acceptable Indoor Air Quality" (or a standard that offers equal or better protection), or if mechanical ventilation is not practical, natural ventilation as long as the concentration of air contaminants, temperature, and relative humidity do not exceed the levels in the ANSI/ASHRAE standard 62.1-2010.
- A ventilation system prevents the return of exhausted air through the outside air intake.
- Exhausted air is replaced by air that:
- Does not constitute a hazard to employee health.
- Does not contain air contaminants in concentrations that exceed 10% of the the occupational exposure limits (OEL).
- Is at a minimum temperature, when necessary (see temperature below).
- Is properly distributed to not cause undue drafts or disturbance of conditions in the workplace.
Regarding temperature, as an employer you must ensure that:
- The temperature where an employee works in an enclosed work area is maintained as follows:
- Where light work is performed while sitting, the minimum temperature required is 20°C.
- Where light physical work is performed while sitting, the minimum temperature is 18°C.
- Where light or moderate physical work is performed while standing, the minimum temperature required is 16°C.
- Where heavy physical work is performed while standing, the minimum temperature required is 12°C.
- When it is impractical to heat an area to the required minimum temperature, that a suitable area is provided where employees can go to get warm.
Regarding air contaminants, as an employer you must ensure that:
- Any air contaminant is kept at a level that does not pose a hazard to an employee and, where a OEL exists, that the exposure of an employee at no time exceeds the OEL.
- Engineering controls are designed, installed, and maintained according to good engineering practices.
- A respirator is provided to an employee, and the employee wears the respirator when engineering controls are not practical or when the engineering controls are being installed.
- When ventilation is used as an engineering control, the air contaminant is controlled at the source by an effective local exhaust ventilation system.
- If local exhaust ventilation is not possible, use general ventilation or a combination of general and local exhaust ventilation.
- A local exhaust ventilation system is designed so that under normal work conditions, the employee’s breathing zone is not in between the source of contamination and the exhaust uptake.
- The ventilation system is not obstructed or blocked by any material or equipment that is placed in front of the ventilation openings.
- The local exhaust ventilation system stays working until the operation or work process is completed and the air contaminants generated are at a level that is not a hazard.
- The local exhaust ventilation system is regularly inspected and monitored to make sure it stays effective.
- If failure of the local exhaust ventilation system may result in a hazard that is not easily noticed by affected employees, equip with a device or other method that will warn of a system failure.
- Provide an adequate supply of makeup air to maintain the effectiveness of the system and prevent air contaminants from being drawn into the work area from another area.
- If a ventilation system discharges air from the work area, the exhausted air must not be recaptured by the fresh (outside) air intake. Any make up air must meet the stated requirements.
- The make up air must:
- Not be a hazard to the health of workers.
- Not contain air contaminants that are more than 10% of the OEL value.
- Be heated, when necessary, to maintain the minimum temperature as needed.
- Be properly distributed in a way that does not create drafts or air disturbances.
- If an operation or work process produces a combustible or flammable air contaminant that is at a concentration that is a risk for fire or explosion, provide a separate exhaust system.
- Electrical components of an exhaust ventilation system must meet the requirements of CSA Standard, C22.1-18 “Canadian Electrical Code, Part 1”, as amended, if the components contact the air flow of the exhaust ventilation system.
- On or after April 1, 2024, a dust collector that has an internal volume of more than 0.6 m3 that is used to control combustible dusts is located so that employees will not be in danger if there is an explosion inside the collector.
- When it can be reasonably expected to be a danger, make sure that exhaust from any internal combustion engine operated indoors is vented to the outdoors.
- When internal combustion engines are operated indoors (such as those on powered mobile equipment or industrial lift trucks), assess the work area for potential exposure to exhaust contaminants, and reduce the concentration of contaminants by adequately servicing and maintaining the engine.
- When regularly operated indoors, any powered mobile equipment, industrial lift truck, or other equipment powered by an internal combustion engine that is manufactured after April 1, 2024, must be equipped with an emission control system or a scrubber.
- If you or your employee has reason to believe that the level of concentration of an air contaminant may be approaching 50% of the OEL, the air is tested to determine the contaminant’s concentration level.
- When employee exposure to an air contaminant occurs in a timeframe other than an eight-hour work day within a 40-hour work week, that the Brief and Scala model (ACGIH publication 2016 Threshold Limit Values for Chemical Substances and Physical Agents and Biological Exposure Indices) is used to adjust the OEL and that employee exposure to the air contaminant does not exceed the adjusted OEL. Also, there must be appropriate medical surveillance of employees exposed to the air contaminants for at least 12 months after the OELs for the air contaminants have been adjusted. While you as an employer must provide for a medical surveillance program, your employees have the option to participate.
- Adequate respiratory protective equipment is provided to each employee where:
- The level of concentration of an air contaminant could exceed 50% of the OEL under normal working conditions.
- There is the possibility of accidental exposure to concentration exceeding the OEL.
- The oxygen content is less than or may be less than 19.5%.
- When work is completed in an area where dust may create a hazard to employees, controls are in place to protect employees.
While the employer is ultimately responsible for all the provisions mentioned above, the supervisor has a vital role to play in the safety of their teams. As a supervisor, you must:
- Acquaint your employees with the hazards and control measures associated with their work.
- Provide the information and instruction necessary to ensure their health and safety.
- Enforce company safety rules, programs, codes of practice and procedures, including ensuring employees comply with the requirements below.
As an employee, you must:
- Follow any instruction, education or training provided by your employer about air quality, and use any equipment that is required (including personal protective equipment).
- Be aware of changing conditions.
- Report any hazards to your employer or supervisor.
(a) except with respect to lead sulfide, formaldehyde, sulphur dioxide, hydrogen sulphide and nitrogen dioxide and any other air contaminant for which the Commission sets an exposure limit, a threshold limit value adopted by the ACGIH and set out in the ACGIH publication entitled “2016 Threshold Limit Values for Chemical Substances and Physical Agents and Biological Exposure Indices”,
(b) with respect to lead sulfide, an exposure limit set at 0.15 mg/m3 - TWA,
(c) with respect to formaldehyde, an exposure limit set at 0.5 ppm - TWA and 1.5 ppm - STEL,
(d) with respect to sulphur dioxide, an exposure limit set at 2 ppm (5.2 mg/m3) – TWA and 5 ppm 00(13 mg/m3) - STEL,
(e) with respect to hydrogen sulphide, a ceiling of 10 ppm (13.9 mg/m3),
(f) with respect to nitrogen dioxide, an exposure limit set at 3 ppm (5.6 mg/m3) – TWA and 5 ppm 9.4 mg/m3) – STEL, and
with respect to any other air contaminant for which the Commission sets an exposure limit, the exposure limit set by the Commission;
Such as, sitting to control machines, performing light hand or arm work while sitting, mental work, precision work, reading or writing, occasional walking, driving.
Such as, sitting to complete tasks, performing hand light hand or arm work (electric machine sewing or work with small machine tools).
Such as, performing light to moderate hand or arm work (using a table saw, scrubbing while standing), walking at a normal pace, machine tool work, assembly work or trimming.
Such as, shovelling, manual sawing, carrying materials, pushing/pulling heavy loads, walking at a fast pace, drilling or manual work with heavy tools.
Viewing CSA Standards as Referenced in NB Legislation
Certain CSA standards are available for online viewing or purchase from the CSA Group.
To access these, you must first create an account with CSA Communities
Once you are logged in, click on the "OHS Standards / View Access" option.
Click on New Brunswick to see the CSA Standards as referenced in N.B. legislation.
The Brief and Scala model provides a reduction factor via the following formula:
Reduction Factor = (8 x hours worked in shift) x ((24 – hours worked in shift) / 16)
It should be noted that the Brief and Scala model should not be used to justify very high exposures for short durations.
Other models may be more suitable and can be used provided a deviation is requested and granted.
https://www.ccohs.ca/oshanswers/hsprograms/occ_hygiene/occ_exposure_limits.html
General Regulation - Occupational Health and Safety Act
N.B. Reg. 91-191
Part III INDOOR AIR QUALITY
Section 18
18. (1) Sections 19, 20, 21, 24, 24.1and 25 do not apply to an underground mine.
(2) Sections 19, 20, 24, 24.1, 25 and 25.2 do not apply to a confined space under Part XVII.
(3) Sections 19, 20, 24, 24.1, and 25.2 and paragraph 22(a) do not apply where a firefighter is engaged in structural fire-fighting.
[N.B. Reg. 96-106, s. 2; 97-121, s. 5; 2001-33, s. 5; 2010-129, s. 1]
Section 20 Ventilation
20. (1) An employer shall ensure that a place of employment is adequately ventilated by
(a) if the place of employment is a health care facility, mechanical ventilation conforming to CSA standard Z317.2 -10, "Special requirements for heating, ventilation and air-conditioning (HVAC) systems in health care facilities" (R2015) or a standard offering equivalent or better protection, and
(b) if the place of employment is not a health care facility and
(i) mechanical ventilation is practical, mechanical ventilation conforming to ANSI/ASHRAE standard 62.1-2010 "Ventilation for Acceptable Indoor Air Quality" or a standard offering equivalent or better protection, and
(ii) mechanical ventilation is not practical, natural ventilation as long as the concentration of air contaminants, ambient temperature and relative humidity do not exceed levels stipulated in ANSI/ ASHRAE standard 62.1-2010 "Ventilation for Acceptable Indoor Air Quality" or a standard offering equivalent or better protection.
(2) Repealed. [N.B. Reg. 2022-27, s. 6]
(3) An employer shall ensure that a ventilation system prevents the return of exhausted air through the outside air intake.
(4) An employer shall ensure that exhausted air is replaced by air that
(a) does not constitute a hazard to the health of employees,
(b) does not contain air contaminants in concentrations that exceed 10% of the occupational exposure limits,
(c) is heated, when necessary, to maintain the minimum temperature specified in section 21, and
(d) is properly distributed so as not to cause undue drafts or disturbance of conditions.
[N.B. Reg. 2022-27, s. 6; 2022-79, s. 2]
Section 21 Temperature
21. (1) Subject to subsection (2), an employer shall ensure that the temperature of a work area in an enclosed place of employment is maintained as follows:
(a) where light work is performed while sitting, such as any mental work, precision work, reading or writing, the minimum temperature required is 20°C;
(b) where light physical work is performed while sitting, such as electric machine sewing or work with small machine tools, the minimum temperature required is 18°C;
(c) where light or moderate physical work is performed while standing, such as machine tool work, assembly work or trimming, the minimum temperature required is 16°C; and
(d) where heavy physical work is performed while standing, such as drilling or manual work with heavy tools, the minimum temperature required is 12°C.
(2) If is not practical to heat a work area to the temperature required by subsection (1), an employer shall provide a suitable place where the employee may go to get warmed.
[N.B. Reg. 2022-27, s. 7]
Section 24 Air Contaminants and Industrial Ventilation
24. (1) An employer shall ensure that an air contaminant is kept at a level of concentration that does not constitute a hazard to the health or safety of an employee exposed to it and, if an occupational exposure limit exists in respect of an air contaminant, that the exposure of the employee to the air contaminant at no time exceeds the occupational exposure limit.
(2) Where the installation of engineering controls is practical, an employer shall install and use appropriate engineering controls to comply with subsection (1).
(2.1) An employer shall ensure that the engineering controls referred to in subsection (2) are designed, installed and maintained in accordance with good engineering practices.
(2.11) An employer shall provide a respirator to an employee and the employee shall wear the respirator in the following circumstances:
(a) the installation of engineering controls is not practical; or
(b) engineering controls are in the process of being installed.
(2.2) An employer shall ensure that if ventilation is used as an engineering control, an air contaminant shall be controlled at the source by an effective local exhaust ventilation system.
(2.21) If local exhaust ventilation is not practical, an employer shall ensure that general ventilation or a com bination of general and local exhaust ventilation is used.
(2.3) An employer shall ensure that a local exhaust ventilation system is designed so that under normal work conditions an employee’s breathing zone is not located between the source of contamination and the exhaust uptake.
(2.31) An employer shall ensure that a ventilation system is not obstructed by material or equipment placed in front of the ventilation openings.
(2.4) An employer shall ensure that an exhaust ventilation system used to control air contaminants in the work area remains in operation until the operation or work process is completed and the air contaminants generated are kept at a level of concentration that does not constitute a hazard to the health or safety of employees.
(2.41) An employer shall ensure that an exhaust ventilation system used to control air contaminants in the work area is regularly inspected and monitored to ensure that the system remains effective.
(2.5) If failure of an exhaust ventilation system could result in a hazard that is not readily apparent to affected employees, an employer shall ensure that the system is equipped with a device or other means to warn employees in the event of a system failure.
(2.51) An employer shall ensure that an adequate supply of makeup air is provided to an exhaust ventilation system
(a) to maintain the effectiveness of the system, and
(b) to prevent an air contaminant from being drawn into the work area from another area.
(2.6) An employer shall ensure that a ventilation system that discharges air from a work area shall comply with the requirements set out in subsections 20(3) and (4).
(2.61) If an operation or work process produces a combustible or flammable air contaminant in concentrations that may present a risk of fire or explosion, the employer shall provide a separate exhaust ventilation system for the operation or work process.
(2.7) An employer shall ensure that the electrical components of an exhaust ventilation system comply with the requirements of CSA standard C22.1-18, "Canadian Electrical Code, Part 1", as amended from time to time, if the components are in contact with the air flow of the exhaust ventilation system.
(2.71) On or after April 1, 2024, an employer shall ensure that a dust collector that has an internal volume greater than 0.6 m3 and is used to control combustible dusts is located and constructed so that no employee will be endangered in the event of an explosion inside the collector.
(2.8) When it is reasonably expected to present a danger to employees, an employer shall ensure that exhaust from any internal combustion engine operated in an enclosed place of employment is vented to the outdoors.
(2.81) When powered mobile equipment, industrial lift trucks or other equipment powered by internal combustion engines are operated in an enclosed place of employment, an employer shall ensure that
(a) the engine is adequately serviced and maintained to minimize the concentration of air contaminants in the exhaust, and
(b) the place of employment is assessed to determine the potential for exposure of employees to harmful concentration levels of air contaminants in the exhaust.
(2.9) An employer shall ensure that any powered mobile equipment, industrial lift truck or other equipment powered by internal combustion engines that is manufactured after April 1, 2024, and is regularly operated in an enclosed place of employment is
(a) equipped with an emission control system that includes feedback control for air/fuel ratio and a three-way catalytic converter, or other equivalent measures, if the powered mobile equipment, industrial lift truck or other equipment is powered by gasoline, propane or natural gas, or
(b) equipped with a scrubber or other emission control system that reduces particulate emissions by at least 70% when tested in accordance with the procedures established by the Mine Safety and Health Administration, US Department of Labor, or a standard offering equivalent or better protection, if the powered mobile equipment, industrial lift truck or other equipment is powered by diesel fuel.
(3) Repealed. [N.B. Reg. 2022-27, s. 13]
(4) Where an employer or an employee has reason to believe that the level of concentration of an air contaminant may be approaching 50% of the occupational exposure limit, the employer shall ensure that the air is tested to determine the level of concentration of the air contaminant.
[N.B. Reg. 2022-27, s. 13]